華中數控銑床對刀方法探討
2021-7-2 來源: 達州職業技術學院機電工程系 作者:陽濤
摘要:數控銑床加工前必須對刀,不同的數控系統對刀的方法也有所不同。基于此,以華中數控 HNC210B 為例,闡述了數控銑床對刀的指令、方法和對刀過程。
關鍵詞:對刀;工件坐標系;G54
數控銑床在加工之前必須進行對刀,否則數控系統無法識別編程人員設定的工件坐標系,也就無法進行正常加工。對于同一個零件的加工,不同的編程人員設定的工件坐標系原點可能不同,因此對刀時的步驟和設定方法也不同。本文以華中數控 HNC-210B 為例,說明數控銑床對刀的不同方法和步驟。
1、對刀的不同指令
對刀任務為設定如圖 1 所示的工件上表面中心點作為工件坐標系原點(編程原點)。
1.1 使用坐標系設定指令 G92 對刀
1.1.1 格式
格式為:G92 X_Y_Z_。其中,X、Y、Z 為刀具刀位
點相對于工件坐標系原點的坐標。
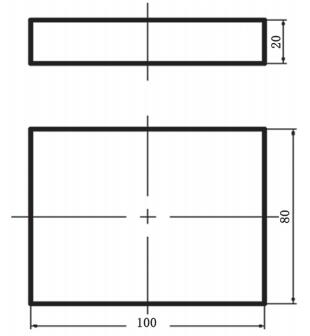
圖 1 工件坐標系原點圖
1.1.2 操作方法
使用手輪方式使刀具與工件左側接觸(看到有少量切屑即可,也可以使用尋邊器),記下此時的機床實際 X 坐標;再使刀具與工件右側接觸,同樣記下此時的機床實際 X 坐標;算出兩個 X 坐標的平均值,即為工件上表面中心點的X 坐標。同理,使刀具接觸工件的前側和后側,可以算出工件上表面中心點的 Y 坐標。再使刀具與工件上表面接觸(也可以采用 Z 軸對刀器),記下此時的機床實際 Z 坐標,即為工件上表面中心點的 Z 坐標,最后移動刀具使其機床實際坐標到達前面算出的 X、Y、Z 坐標,也就是刀具位于了工件坐標系原點,因此刀具的刀位點相當于工件坐標系原點的坐標是(0,0,0),則程序中的指令為:G92 X0 Y0 Z0。
但是加工之前,刀具與工件之間不能接觸,要有一定距離,比如刀具在工件坐標系原點正上方 100mm,則刀具移動的 Z 坐標要在原來的基礎上加上 100mm,故刀具的刀位點相當于工件坐標系原點的坐標是(0,0,100),則程序中的指令為:G92 X0 Y0 Z100。要注意的是,在加工之前刀具不能再移動,否則建立的工件坐標系會被破壞,無法進行正常加工,這對于操作人員將十分不方便,并且還需要操作人員自己算出平均值,比較麻煩,因此一般情況下不會采用 G92 指令設定工件坐標系。操作步驟示意如圖 2 所示。
1.2 使用工件坐標系選擇指令 G54 ~ G59 對刀
1.2.1 格式
格式為:G54/G55/G56/G57/G58/G59。
1.2.2 操作方法
按操作面板上“設置”→“坐標系”對應功能鍵,進入如圖 3 所示的坐標系界面,通過光標鍵及翻頁鍵在G54 ~ G59 中選擇,以選擇 G54 為例。使用手輪方式使刀具與工件左側接觸,將光標移動到 G54 的 X 位置,如圖 3所示,按下界面最后一行的“記錄Ⅰ”,再使刀具與工件右側接觸,按下界面最后一行的“記錄Ⅱ”,再按下界面最后一行的“分中”,則確定了 G54 的 X 坐標,將光標移動到 G54 的 Y 位置,同理可以確定 G54 的 Y 坐標。最后使刀具與工件上表面接觸,按下界面最后一行的“當前位置”,注意在確定 Z 坐標前要將光標移動到 G54 的 Z 位置。程序中的指令中加入 G54,數控系統會自動調用 G54 存入的 X、Y、Z 值。由于 G54 ~ G59 對刀操作簡單,不需要
操作人員計算平均值,并且加工之前刀具可以任意移動,因此通常情況下都采用 G54 ~ G59 方式對刀。
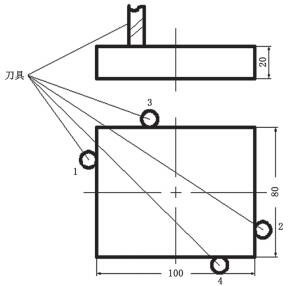
圖 2 刀具操作步驟示意圖
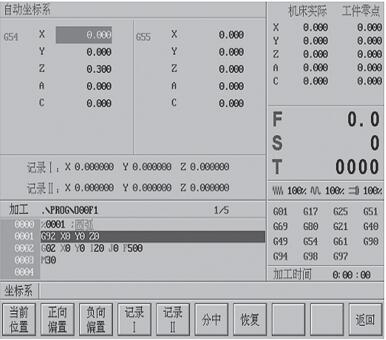
圖 3 坐標系界面
2、同一工件不同工件坐標系的對刀
上述對刀任務選擇的是工件上表面中心作為工件坐標系原點,而不同的編程人員選擇的工件坐標系原點可能不同,還可以選擇上表面的 4 個角點作為工件坐標系原點。
2.1 以工件上表面的左上角作為工件坐標系原點
如圖 4,使刀具接觸工件的左側和前側,由于刀具中心與工件坐標系原點相差一個刀具半徑值,因此需要偏置。由圖可知,工件坐標系原點處于左側刀具的右邊(+X 方向),故 G54 的 X 坐標應該加上刀具半徑值,工件坐標系原點處于前側刀具的后邊(-Y 方向),故 G54 的 Y 坐標應該減去刀具半徑值。加上或減去刀具半徑值可以通過圖 3 中最后一行的“正向偏置”“負向偏置”來進行。如要加上半徑值,按“正向偏置”,輸入半徑值后回車即可;如要減去半徑值,按“負向偏置”,輸入半徑值后回車即可。
2.2 以工件上表面的右上角作為工件坐標系原點
同理,如圖 5,G54 的 X 坐標應減去刀具半徑值,G54的 Y 坐標應減去刀具半徑值。
2.3 以工件上表面的右下角作為工件坐標系原點
同理,如圖 6,G54 的 X 坐標應減去刀具半徑值,G54的 Y 坐標應加上刀具半徑值。
2.4 以工件上表面的左下角作為工件坐標系原點
同理,如圖 7,G54 的 X 坐標應加上刀具半徑值,G54的 Y 坐標應加上刀具半徑值。
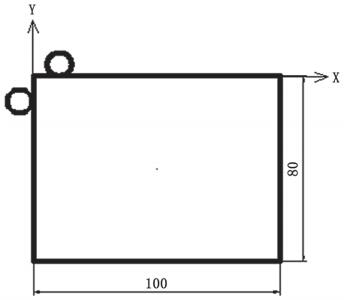
圖 4 刀具中心與工件坐標系原點偏置 1
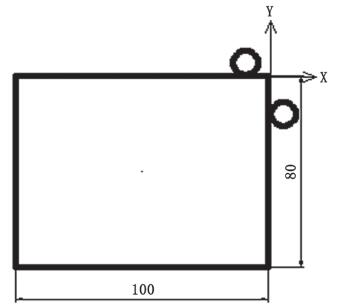
圖 5 刀具中心與工件坐標系原點偏置 2
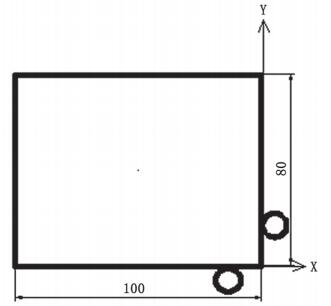
圖 6 刀具中心與工件坐標系原點偏置 3
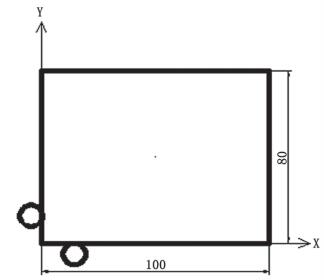
圖 7 刀具中心與工件坐標系原點偏置 4
3、多把刀具的 Z 向對刀
數控銑床加工中,經常會使用多把不同的刀具加工同一個零件,理論上每一把刀具都需要對刀。對于加工同一個零件,每一把刀裝夾到主軸上時,刀具的軸心線都是同軸的,因此只需要對標準刀進行 X 向和 Y 向對刀,其他刀
具不需要對 X 向和 Y 向,使用和標準刀相同的對刀值即可。每一把刀裝夾到主軸上的長度不同,因此每一把刀的 Z 向必須對刀。如果把每一把刀所對的 Z 值都記下來,然后在使用每一把刀之前將 G54 的 Z 值進行修改,則非常麻煩,并且耽誤時間,效率低。為了提高效率,可以采用刀具長度補償的方法進行 Z 向對刀。
3.1 每一把刀都進行長度補償的 Z 向對刀(絕對坐標)
將 G54 的 Z 值輸入零,按“刀補”中的“刀補表”鍵,進入如圖 8 所示的界面,然后將每一把刀所對的 Z 值輸入到長度補償里。
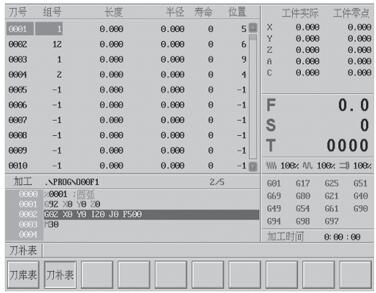
圖 8 補刀表界面
3.2 設置標準刀進行長度補償的 Z 向對刀(相對坐標)
將 G54 的 Z 值輸入一號刀(標準刀)對應的 Z 值,按“刀補”中的“刀補表”鍵,進入如圖 8 所示的界面,一號刀的長度補償值輸入零,其他刀的長度補償值輸入其與一號刀的長度差值。長度差值確定方法:一號刀與工件上表面接觸,按“設置”中的“相對清零”鍵,進入如圖 9 所示的界面,按“Z 軸清零”,再換成其他刀具,同樣使刀具與工件上表面接觸,屏幕上顯示的 Z 軸相對實際坐標即為長度差值。
4、刀具折斷后的對刀
數控銑削加工中會出現刀具折斷的情況,特別是精加工時采用直徑很小的刀具時,如果切削參數設置不合理,很容易斷刀。斷刀后,對刀的表面已經被切掉,因此可以利用 Z 軸對刀器對新刀具進行 Z 向對刀(X 向和 Y 向不需要對刀),如圖 10 所示。
4.1 絕對坐標方式
將 Z 軸對刀器平放在工件上或平口鉗上,先用標準刀與 Z 軸對刀器上表面接觸(Z 軸對刀器指針指到零),記下此時的 Z 坐 標( 如 -388.5mm); 再換成新刀具,同樣使其與 Z 軸對刀器上表面接觸,記下此時的 Z 坐標(如 -408.5mm),則兩者的差值為 -20mm。再計算標準刀與斷刀的長度補償差值,如為 -22.5mm,兩個差值求差為 2.5mm,說明新刀比斷刀長了 2.5mm,則新刀的長度補償值應為斷刀長度補償值(如 -308.6mm)的基礎上加上2.5mm。此方法比較繁瑣,也容易出錯,故一般不用。
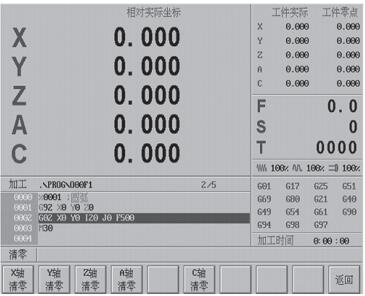
圖 9 清零界面
4.2 相對坐標方式
將 Z 軸對刀器平放在工件上或平口鉗上,先用標準刀與 Z 軸對刀器上表面接觸(Z 軸對刀器指針指到零),按“設置”中的“相對清零”鍵,按“Z 軸清零”,再換成新刀具,同樣使其與 Z 軸對刀器上表面接觸,屏幕上顯示的 Z 軸相對實際坐標就是長度差值,將其輸入到對應的長度補償值里即可。這種方法不用計算,操作非常簡單。
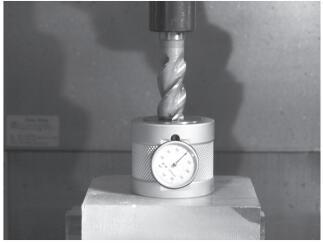
圖 10 刀具折斷后的對刀圖
5、結語
對于不同的操作人員和不同的數控系統,數控銑床的對刀方法不盡相同。在實際操作過程中通過不斷摸索,選擇操作最簡單、最不容易出錯的方法對刀,可以起到事半功倍的效果。
投稿箱:
如果您有機床行業、企業相關新聞稿件發表,或進行資訊合作,歡迎聯系本網編輯部, 郵箱:skjcsc@vip.sina.com
如果您有機床行業、企業相關新聞稿件發表,或進行資訊合作,歡迎聯系本網編輯部, 郵箱:skjcsc@vip.sina.com