數控機床虛擬裝配系統的研究
2025-4-10 來源:南京工業大學工程訓練中心 作者:馬康榮
1.引言
在現代機械制造業中,數控機床作為核心裝備之一,其性能與制造精度直接影響著工業生產的效率和產品的質量。隨著全球市場競爭的加劇及技術進步的推動,中國機械制造業邁向數字化、定制化和智能化的新階段。此背景下,傳統的數控機床設計與裝配流程面臨著諸多挑戰,尤其是設計周期延長和裝配校驗成本提高等問題已成為制約行業發展的瓶頸。因此探索一種能夠提高設計效率、降低裝配成本并確保機床性能的新技術尤為迫切。
2. 數控機床虛擬裝配系統總體設計
2.1 系統結構設計
在數控機床虛擬裝配系統的研發過程中,系統結構設計扮演了至關重要的基礎性角色(圖 1)。
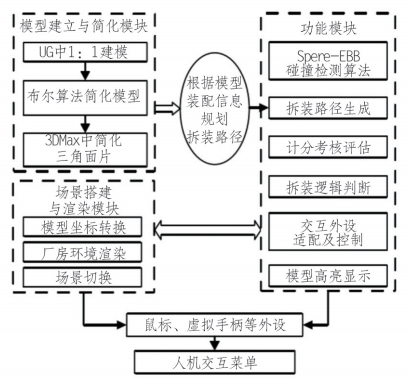
圖 1 系統整體結構
系統旨在構建一個跨平臺兼容、用戶友好的虛擬裝配環境,通過高度的沉浸感和直觀高效的操作體驗,提升用戶工作效率。為達到這一目標,系統被細分為 4 個核心模塊 : 模型建立與簡化模塊、場景搭建與渲然模塊、功能模塊和人機交互模塊。
場景搭建與渲染模塊負責將模型放置于接近現實的虛擬環境中,通過光源等渲染技術增強場景的真實感,為功能模塊的實施提供視覺基礎,確保用戶體驗既真實又舒適。
系統的核心組成部分是功能模塊,其集成裝配路徑規劃、零件拆卸與拾取等關鍵操作,在嚴格遵循機械工藝標準的基礎上,設計并生成最佳的裝配路徑。為提高操作的精確度和響應速度,模塊中引入碰撞檢測機制。此外,功能模塊還包含多功能區域,例如演示、練習和考試評估,以滿足不同用戶群體的訓練和評價需求。
人機交互模塊負責實現場景的無縫漫游和切換。通過融合 Steam VR 插件,用戶可以利用頭戴式顯示器和 Vive 操控器,從第一人稱視角進行場景探索和零件操縱。這一設計極大地提升了用戶的沉浸感和操作的直觀性。
2.2 系統設計方法
在數控機床虛擬裝配系統的實現研究中,為確保最終系統功能完備、用戶沉浸感強,系統設計方法須具備科學性和合理性。本研究采用Unity 3D 作為開發引擎,詳細規劃了從模型構建到最終系統集成與發布的全過程,系統搭建框架如圖 2 所示。首先,采用 UG(現稱為 NX)軟件對目標數控機床進行 1:1 的精確測繪工作,確保模型的幾何精度與實物相符合。完成測繪后,將模型以標準轉換協議格式 STEP 導出。隨后,將所得的 STEP 格式模型引入至 3D Max 軟件環境中,進行必要的優化處理。這一階段主要移除模型中存在的冗余幾何元素,包括非必要的多層面等,以及為模型賦予適當的材料和紋理,進行渲染處理,從而提升視覺效果,確保模型在虛擬環境中的真實性和逼真度 。
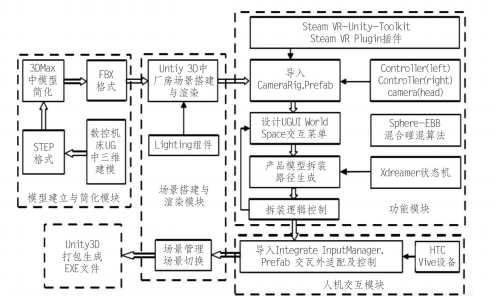
圖 2 系統框架搭建
3. 數控機床虛擬系統三維模型建構
3.1 機床模型建構
在數控機床虛擬裝配系統的開發研究中,機床模型的構建是系統的基礎和核心要素。三維建模技術在此過程中發揮了重要作用,它運用計算機圖形學技術,精確地復制現實物體的幾何結構和表面特征,以創造出高度逼真的復雜三維模型。在高度精細的虛擬仿真領域構建三維環境,包含各種廠房、拆卸工具和設備。這些建筑和工具以精確的三維模型形式呈現,其真實度直接影響用戶沉浸感的強度及整個系統交互性能的優劣。
通過實地測量、綜合分析相關文獻資料,精心捕捉實體設備的準確尺寸、外觀顏色和材料特性等關鍵信息。利用專業建模軟件進行幾何結構的精確復制,并根據應用需求設定相應的約束條件。為降低系統資源消耗,對模型的頂點數量和三角面片數量進行優化 ; 為增強現實感,向模型中添加物理屬性,包括重力和加速度。本研究選擇了 UG 軟件來構建數控機床模型,該軟件在處理復雜實體和造型方面具有顯著優勢,并支持多種建模技術的融合。
數控機床采用自底向上的方法,先構建基礎零件,再逐步組裝成上一級部件,最終完成整個機床的裝配。這種方法有助于提高裝配效率,簡化裝配路徑規劃,并防止在零件繪制過程中出現遺漏。在機械裝配工藝中,必須注意使用標準工具避免損害精密零件 ; 緊固螺栓時應均勻對稱操作 ; 所有電氣元件的導線接頭需做好標記。依據實物數據,將零件模型拆解并分層級,利用多邊形編輯和高級命令生成簡單幾何體,然后通過布爾算法構建復雜零件。
3.2 機床碰撞檢測算法
混合層次包圍盒算法(Hybrid HierarchicalBounding Volume Algorithm)是一種先進的碰撞檢測技術,其在構造包圍盒樹時,通過融合多種包圍盒的互補特性,于樹的不同層級上部署不同性能的包圍盒。該算法的設計旨在提升碰撞檢測的準確性和效率,有效避免模型間的相互穿透問題。
算法的實施過程可劃分為 3 個關鍵階段 : 預處理、初步檢測和精確檢測。
在預處理階段,算法涉及包圍盒的選擇,這一步驟需要考慮到包圍盒的幾何特性、系統資源配置及模型的特定屬性。在此基礎上,精心規劃邊界體積層次結構(Bounding VolumeHierarchy,BVH)的結構設計和遍歷策略,以確保高效的碰撞查詢性能。
在初步檢測階段,算法利用所選包圍盒進行快速排除測試,以減少后續階段需要處理的候選物體數量。在此過程中,選擇球形(Sphere)包圍盒作為根節點的包圍體,其優勢在于能夠迅速排除大量不相交的物體,顯著降低三角基元的檢測負擔。
在精確檢測階段,進行算法執行包圍盒間及三角形基元間的詳細相交測試,確保碰撞檢測的高精度性。
包圍盒層次結構樹的構建策略主要有 3 種 :自頂向下、自底向上和插入法。
(1)自頂向下的策略是最為廣泛采用的構建方法,其核心在于遞歸算法的應用。這一策略的構建過程在邏輯上模擬了自然界中樹木的生長機制。在具體操作過程中,首先選擇包含整個模型所有幾何信息最外層的包圍盒作為層次結構樹的根節點。依據樹的平衡原則和相關數據信息,通過遞歸的方式將根節點劃分為多個子集,這些子集作為父節點即 “分叉”,繼續對各個子節點進行遞歸劃分,直至達到葉節點,即一個三角形基本元素。
(2)自底向上的策略主要通過聚類合并算法來實現構建。在初始階段,需要對模型的三維數據進行全面處理,獲取全部三角基本元素的信息。針對每一個基本元素構建出最緊密的包圍盒,作為包圍盒層次結構樹的底層葉節點。根據三角基本元素間的相關性,將多個葉節點進行聚類,逐步合并為一個新的子節點,然后繼續進行節點類的合并,直至形成根節點。
(3)插入法主要是根據成本函數,將單個三角基本元素按照最低成本插入到樹型結構的節點處。通過不斷重復此過程,將每個基本元素進行填充,最終構建出成本最低的包圍盒層次結構樹。
4. 數控機床虛擬裝配系統的實現
4.1 人機交互實現
在數控機床虛擬裝配系統的開發過程中,人機交互的科學設計及精確實現對提升用戶體驗、增強系統實用性具有決定性作用。該系統融合了多種輸入設備,包括鼠標、觸屏及虛擬現實(VR)手柄,以實現一系列豐富的交互功能。系統的人機交互設計支持多硬件平臺,包括智能手機、電腦 PC 端和 VR 設備,確保了使用方式的多樣性和廣泛的可訪問性。用戶可以通過不同的設備執行操作,例如進行場景切換、狀態機響應和碰撞反饋等。
碰撞反饋機制通過Unity 3D 的射線和Gameobject 組件來實現。當模型間發生接觸時,系統會提供文字提示,從而增強操作的直觀性和指導性。此外,人機界面的設計采用 UGUI 系統,不僅直觀易用,而且允許開發人員在運行過程中實時調整 UI 元素,從而提高開發效率和界面的適應性。整個系統的人機交互實現經過精心規劃與設計,使得數控機床虛擬裝配系統不僅具備強大的功能,還擁有友好的用戶界面,確保用戶能夠輕松地與系統進行高效交互。這種交互設計的深度與廣度為用戶提供了一個高度逼真、互動性強的虛擬裝配環境。
4.2 功能模塊實現
基于數控機床的裝配結構樹和位置約束,可以制作符合實際工藝的拆卸動畫。在 Unity 3D中,使用 Animation 控件的關鍵幀功能來關聯各個動畫,完成制作。以縱向進給系統為例,先根據機械規則和幾何建模信息逆序求解拆卸序列,然后從零件庫中調用所需的模型和工具,并設置時間區間、路徑、偏移等參數。
用戶可通過點擊 “演示” 按鈕進入功能界面。界面提供時間軸播放器、步驟列表等提示框,以便輔助學習拆卸過程。系統集成了人機交互的手柄功能按鍵,包括觸控板、菜單按鈕等。用戶可以通過手柄控制器上的腳本實現自主漫游。
虛擬裝配功能使用 C++ 語言編寫碰撞檢測算法,并與后臺進行集成。在選中零件時,系統進行預處理,讀取三角面片的頂點索引,并生成包圍盒層次樹。當發生碰撞時,系統讀取 ID 信息,并將其反饋到文本框中。圖 3 所示的手輪觸碰尾架蓋時,系統會做出相應的響應,并彈出提示框,以指導用戶的操作,提升其實操能力。
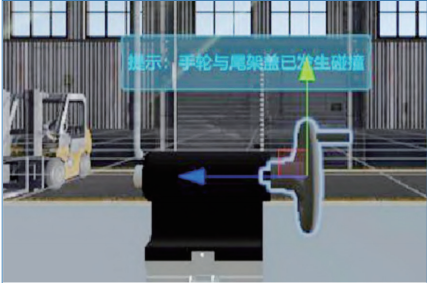
圖 3 零件發生碰撞效果
5. 結束語
本次研究成功實現數控機床虛擬裝配系統的功能模塊搭建 : 首先,進行數控機床模型的構建,采用自下而上的裝配層次樹構建方法進行模型建設 ; 其次,基于混合層次包圍盒算法的碰撞檢測技術驗證其在碰撞檢測時間和檢測精度方面的優越性 ; 最后,完成數控機床虛擬裝配系統的設計和實現。通過該系統用戶可以進行真實感的虛擬裝配操作,并獲得實時的反饋和提示信息,提高用戶的實操水平。
投稿箱:
如果您有機床行業、企業相關新聞稿件發表,或進行資訊合作,歡迎聯系本網編輯部, 郵箱:skjcsc@vip.sina.com
如果您有機床行業、企業相關新聞稿件發表,或進行資訊合作,歡迎聯系本網編輯部, 郵箱:skjcsc@vip.sina.com
更多相關信息