多品種微機電伺服機構小直徑銷孔高效加工工藝技術研究
2018-4-13 來源:中北大學 山西省深孔加工工程技術研究中心 作者:張煌,沈興全,李耀明,翟寧
摘 要: 針對微電機軸與配套齒輪副銷孔加工過程中,自動化程度低,定位精度差,成品率低及刀具磨損嚴重等多重問題。深入分析系統工裝特性及產品互換性,優化加工工藝,著重研究產品設計要點。基于深孔加工理論,采用配鉆工藝,創新研制精密高效電機軸與配套齒輪副微銷孔配打專用裝置。通過實驗研究,對比分析工藝優化前后加工銷孔的位置精度和加工效率,驗證優化工藝及裝置的明顯優勢,對實際應用提供良好的指導、借鑒作用。
關鍵詞: 電機軸; 銷孔; 配鉆; 加工工藝; 優化設計; 定位裝夾
在軍事和航空航天領域中的設備裝置需承受高加速產生的慣性附加載荷 。隨著科學技術的迅猛發展,微電子技術、電機制造工藝水平的不斷提高,結構緊湊、性能穩定、效率高的微型伺服電機在航空、航天領域得到了越來越廣泛的應用。
微型伺服電機軸與微小齒輪直接裝配連接,其作為直接驅動部件,在航天某系統中承擔著關鍵性任務。所以,電機軸與配套齒輪副銷孔的精準配合及可靠性保障顯得至關重要,現代加工技術的發展,使得上述要求逐一變為可能。銷孔裝配是機械產品常見的裝配形式,且在特定的性能要求下對銷孔裝配質量要求較高。其不僅影響到產品的位置精度、裝配精度,而且影響到相關裝配件的穩定性、安全性及壽命等。特別對于精密齒輪副的定位,如若銷孔加工誤差大,極易引起齒輪裝配不當,或局部應力集中,甚至齒輪不嚙合,造成動力傳輸失效; 還會引起齒輪副振動明顯,系統穩定性急劇下降。郝長中針對活塞異形銷孔加工,利用磁致伸縮材料特性和彈簧板彈性產生鏜刀的徑向微位移達到設計要求。楊博通過調整機床精度、加工參數實現高精度小直徑定位銷孔的加工.盧娜利用有限元的方法進行了機車電機軸與小齒輪軸配合的模擬分析。張凱基于壓電陶瓷提出了一種新型活塞異形銷孔數控加工方法。史濤、邊境等人采用臥式加工中心,提出了一種新型的齒圈銷孔加工方法。
大多數研究人員對銷孔進行了多方位的研究,但是對于多工件配鉆 方法的研究還極其稀少,其適用工藝還需有針對性研究,將各向功能結構的產品集成于一體,其裝配形式、功能實現便需要新工藝、新技術的保障。本文針對微伺服電機、錐齒輪、軸承集成于一體的結構,完成定位銷孔的加工,深入研究銷孔配鉆加工工藝技術,通過不同工藝的實驗對比,優化加工工藝,創新設計適應多品種、大批量產品的互換性、精密加工要求的裝置。
1 、工件系統特性及工藝優化分析
1. 1 工件系統特性
如圖 1 所示,系統由微伺服電機 1、軸承 5、錐齒輪 6 集成于一體,系統中具有端面凸臺 2 及端面間隙 3,依靠定位銷 4來保證齒輪的高度,并實現動力傳輸。
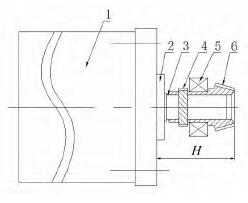
圖 1 微機電伺服機構裝配系統結構
( 1) 因系統裝配集約性,并且微定位銷孔靠近電機端面,再加之軸承的干涉,阻礙了普通裝夾裝置、定位輔助裝置等的應用,導致普通刀具無法滿足加工要求,必須使用加長硬質合金刀具,這無疑使得刀具懸伸太長,剛度系統差。
( 2) 微伺服電機系統固有特性的限制。電機軸不宜承受軸向力,且錐齒輪尾端面與電機端面凸出臺有間隙。
( 3) 針對不同產品定位銷孔的尺寸要求不同,微伺服電機尺寸、外伸軸長、各功能部件的裝配要求也各不相同,這樣使得產品互換性要求較高。
1. 2 傳統工藝分析
傳統的加工工藝,首先在錐齒輪上根據技術要求測量尺寸,并鉆孔; 其次,將錐齒輪、軸承與電機裝配,用膠粘接。等待強力膠起作用后,人工手動利用小型鉆床,逐個工件完成銷孔制作; 最終裝配銷釘,完成系統集成。不難看出其加工效率、精度、可靠性保障等與精密動力系統的嚴格要求,截然背道而馳。
( 1) 自動化程度低,定位精度差,需多次重復測量因普通裝夾、定位系統受到限制,電機的裝夾僅靠人工及測量工具裝夾于臺虎鉗。并需多次重復測量,累積誤差大大增加。由于尋找定位的試鉆凹陷點的存在,鉆頭剛性較差,當高速鉆床主軸轉動,使得再次對刀定位電機徑向軸線時,極易重復定位到凹陷點處,準確定位更加不易。再加之采用的粘接配鉆法,微小零件裝配接觸面積小,可用于涂敷粘膠的表面積相應的也小,施膠量少,連接強度必然受到影響。
(2) 鉆頭易斷,增加了經濟成本電機軸采用高硬度材料,為光滑圓柱形,使得刀具與電機軸徑向軸線難以嚴格同軸,略微的偏斜都會使得電機軸轉動,再加之系統剛度系統差,導致刀具極易折斷,更換鉆頭后又需重復之前工作。
( 3) 效率不高,還需豐富經驗多次不斷重復的測量,找正定位及刀具的易折斷,完成一次鉆孔需要耗費相當多的時間、精力,經濟成本太高,效率太低。人工鉆孔還需要有足夠豐富經驗的操作者才可順利完成。
另外,由于小齒輪的最終裝配高度精度差異大,即一致性、互換性差,導致整機性能也存在一定的差異。
1. 3 工藝優化
針對多品種、多干涉小直徑工藝銷孔的研制,深入分析傳統工藝技術的缺陷,基于深孔加工系統理論,設計研究專用多工位工件裝夾系統、鉆模輔助支撐裝置、氣動定位機構等,采用配鉆工藝對集成于一體的微伺服電機系統完成銷孔加工。
以配鉆工藝一次性完成銷孔的制作代替傳統工藝中的測、粘、固等工序; 以專用鉆模彌補傳統工藝中剛度系統差的缺點; 以送料機構、定位機構、及自動夾緊機構代替原有人工裝夾。既減少了加工工藝,又提高了銷孔的位置精度等級,增加了產品的互換性,實現了從送料,定位,夾緊,加鉆孔為一條龍的自動化連續運轉,因而有效增強加工精密度,提高生產效率。
2 、優化設計
2. 1 設計理論基礎
優化設計中主要考慮工件的定位裝夾、配鉆對工件裝夾穩定性的影響及系統本身固有特性( 電機軸的轉動) 的影響,著重研究麻花鉆的影響效果。而 v型鐵具有天然的自定心性能,主要用來安放軸、套筒、圓盤等圓形工件,以便定位中心線。微電機的外形結構與此不謀而合,故應用 V 型鐵為基準,方便確保工件的精確定位。
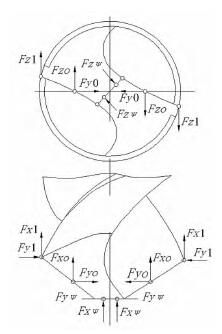
圖 2 麻花鉆切削受力情況

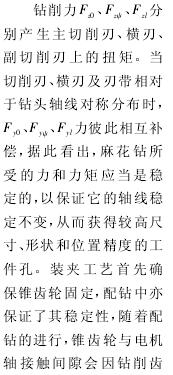
輪后產生的切屑而起到粘固的功用,同時,在設計中確保鉆模中心與電機軸徑向中心線嚴格對齊,以此保證鉆削過程中電機軸的穩定。
2. 2 總體方案設計
精密高效電機軸與配套齒輪副微銷孔配打專用裝置總體方案包括兩部分: 機械系統方案設計和控制系統設計。
其中,專用裝置的機械系統由六工位回轉臺、鉆削動力系統、工件裝夾系統、氣動裝置四個主要部分組成。如圖 3 所示的電機軸與配套齒輪副銷孔配打專用裝置,包括底座 1,其上設有回轉工作臺 3、薄型氣缸 5、鉆削動力系統( 包括豎向同軸的高精度臺鉆 8 和可換式鉆模 10) 和限位組件( 包括鉆模支架 14 和其上水平安裝的限位塊 13) ,回轉工作臺 3 下方設有數控分度盤 2,回轉工作臺 3 上均布設有若干安裝電機 11 的 V 型鐵組件 7,薄型氣缸 5 通過氣缸支架4 固定于底座 1 上。
利用該裝置鉆孔時,首先將要鉆孔的齒輪和 U 型墊 12裝配到需要鉆孔的電機軸上,然后將裝配好的齒輪和電機安置在回轉工作臺 3 的 V 型鐵組件 7 上,利用程序控制回轉盤旋轉,將待鉆孔工件輸送到指定的位置,由薄型氣缸 5 自動輸出作用力推動推桿 6,并組合 U 型墊 12、限位塊 13
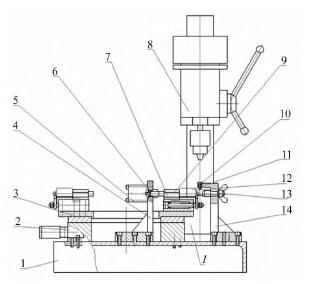
圖 3 系統工作原理示意圖
實現軸向夾緊,精確定位,再通過可換式鉆模 10 精確地實現引導、鉆孔。完成鉆孔后,推桿 6 后撤,彈簧 71 收縮,復位板 74 彈簧恢復原狀( 恢復至初始位置,即沿圖 3 中向左方向復位) ,令裝配好的電機和齒輪歸位,自動回轉盤使下一個需鉆孔的電機和齒輪進入到工作位置。
2. 3 工件裝夾系統的設計
工件裝夾系統在設備中起到至關重要的作用,它不僅要實現工件的快捷、簡便安裝及自動化控制,而且要確保錐齒輪端面與電機安裝面的高度尺寸。同時,還需要實現不同尺寸電機與齒輪要求的裝夾功能,確保鉆頭中心與電機軸中心在同一垂直線上,實現電機與齒輪的自動裝夾。這樣就需要在設計中增加輔助裝置,從而滿足其多樣化功能。為能最方便將配打電機既不做過多調整來滿足不同規格電機的安裝,同時使用同一臺設備。有兩種方案:
( 1) 方案一: 兩種不同規格電機均以 V 型鐵做為定位原件,然而其外形尺寸相差過大,必然導致中心高度變動較大,那么需要同時將氣缸支架、鉆模支架更換或增加調節中心高的裝置; 并且要調節鉆床主軸高度( 鉆床主軸行程所限) 。
( 2) 方案二: 以 V 型鐵做為定位原件,以大型號電機中心高為基準,增加輔助裝置 V 型墊塊,使小型號電機中心與其一致。只需更換鉆套、限位塊和鉆頭即可比較方便的解決兩種不同型號電機在同一鉆床的配鉆工作。
綜合分析上述兩種方案,方案二不至于頻繁的更換鉆模支架,且方案二方便、快捷,明顯優于方案一,因此,結構設計中采用方案二。
2. 3. 1 V 型鐵組件的設計
V 型 鐵 組 件如圖 4、5 所示,包括 V 型 鐵 73 以及水平安裝于 V型鐵 73 下段內的限位 桿 72,限位桿72上套裝有彈簧 71,限位桿 72的懸出端安裝有復位 板 74,復 位板 74 通 過 螺 母75 鎖緊。復位板74 上端作用于電機外殼端面,U 型墊 12 用以保證齒輪的軸向定位。
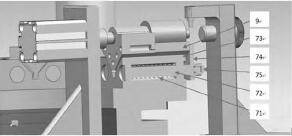
圖 4 小型電機裝夾圖
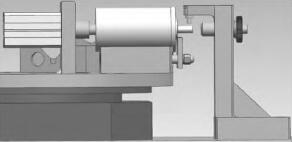
圖 5 大型電機裝夾圖
為實現不同尺寸電機與齒輪要求的裝夾功能,增加產品互換性,設計中采用方案二,以大型電機為基準,以 V 型鐵 7為定位基座,保障其自動定位功能; 小型電機則通過增加 V型墊塊 9 來增加中心高度,從而在不更換氣缸支架 4、鉆模支架 14 的基礎上,使不同尺寸電機的中心高度保持一致。由于齒輪銷孔位置和齒輪端面對電機端面也有要求的差別,不同型號電機的精確定位,只需更換相對應的鉆模 10、U 型墊12、限位塊 13 及刀具,并輔助相應的 V 型墊塊 9 即可。帶有復位功能的 V 型鐵組件,避免了由于操作者的誤安裝,回轉臺轉動后,導致電機與鉆模支架的干涉碰撞。
2 . 3. 2 多工位回轉臺的設計
多工位回轉臺用于將電機齒輪組裝后自動輸送到指定打孔位置。其底座采用數控高精度伺服控制 系 統 分 度盤,回 轉 精 度 達到 0. 01°,分度盤上量 60 度均均布裝有 V 型鐵。使得在回轉臺上一次可裝夾六個工件,當前一個工件加工完畢后,按下切換按鈕,自動切換到下一個工位并自動夾緊工件,可以直接進行下一個工件的加工,節省頻繁更換工件的時間。多工位回轉臺如圖 6 所示。
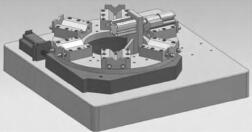
圖 6 多工位回轉臺結構示意圖
2. 3. 3 U 型墊的設計
因電機與齒輪裝配完成后,在電機軸與電機端面結合處有微小凸臺,且齒輪端面與電機端面有間隙高度。此間隙高度決定了齒輪的裝配位置及鉆孔位置,為此設計專用墊片來保障尺寸要求及定位要求。氣缸、U 型墊、齒輪、限位塊組成的軸向夾緊,增加了齒輪前端面與限位塊的摩擦,保證電機前端因鉆削進給力的作用而不至于傾斜,同時,使得錐齒輪得到可靠固定,避免其繞電機軸的轉動。
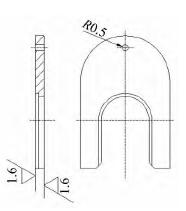
圖 7 U 型墊結構示意圖
3 、實驗分析
實驗針對電機外形直徑為 Φ50 和 Φ29 的兩種型號電機系統,分別利用傳統工藝與優化工藝進行銷孔加工,對比分析兩種加工工藝后的銷孔位置精度和加工效率。實驗條件及具體參數如表 1。
表 1 實驗參數
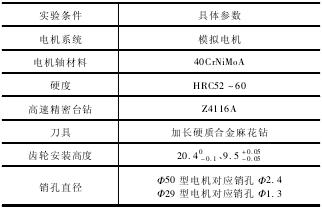
圖 8( a) 為分別利用傳統工藝及優化后工藝對 Φ50 型電機進行配鉆銷孔 Φ2. 4 所得七組實驗結果對比圖,高度值 H為齒輪端面距離電機安裝面的距離。圖 8( b) 為 Φ29
型電機進行配鉆銷孔 Φ1. 3 所得七組實驗結果對比圖。
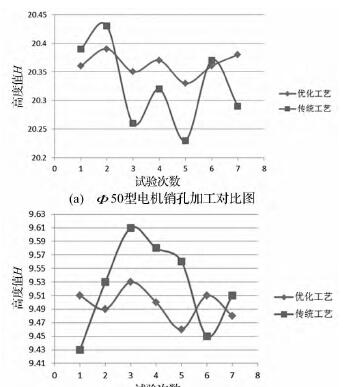
圖 8
從圖 8( a) 、( b) 中均可看出,傳統工藝與優化后工藝存在明顯差距,優化后工藝所測高度值成正態分布于技術要求均值附近波動,微小的波動源于機床系統的固有振動及麻花鉆本身特性所決定。而傳統工藝誤差過大,成品率低。對比分析圖 8( a) 和( b) 可知,傳統工藝完成鉆孔后所得結果無規律,并且隨著銷孔直徑的減小,偏差越大,這主要是由于刀具剛度系統差、工件定位不可靠所導致。
4 、結 論
( 1) 由于刀具剛度系統差、工件定位不可靠,導致擴孔現象、位置精度差、偏差無規律等惡劣現象的發生。
( 2) 為實現在同一臺設備中滿足多品種工件不同要求的加工,增加產品互換性,針對圓柱形工件,利用 V 型鐵來對其進行裝夾定位,以大型工件為基底,通過輔助 V 型墊塊,即便捷又精準。
( 3) 考慮到工件的多樣性、多干涉性,增加鉆模輔助支撐,極大地增強了刀具系統剛度; 以多工位回轉臺并集成工件自動恢復原始狀態功能,實現了工件的高效、精準裝夾及自動化控制。
( 4) 通過對比分析傳統工藝及優化后的實驗效果,驗證了優化工藝的高精度、自動化、簡便快捷、多適應性的優點,對實踐應用提供良好的指導、借鑒作用。
投稿箱:
如果您有機床行業、企業相關新聞稿件發表,或進行資訊合作,歡迎聯系本網編輯部, 郵箱:skjcsc@vip.sina.com
如果您有機床行業、企業相關新聞稿件發表,或進行資訊合作,歡迎聯系本網編輯部, 郵箱:skjcsc@vip.sina.com