大型深孔加工機床在線檢測系統的研究與設計
2018-4-8 來源:廣東工業大學 機電工程 佛山新成洪鼎 作者:劉洲 張平 李新濤 張國根
摘要: 目前大型深孔( d > 500mm,h > 80000mm) 現場加工機床的主軸定位均采用手工卡尺測量或是人工打表等方法,針對這些方法不足的問題,文章開發出了一套在線式自動檢測與加工一體化裝置。該裝置運用激光位移傳感器在線掃描被加工件內腔輪廓,采用互為基準的自動定心方法,應用雙重迭代算法快速得到虛擬軸的空間位置。調整機構的快速響應和檢測元件實時的反饋,使得機床主軸與虛擬軸自動調整重合并進行后續加工。在現場的實際應用表明系統很好地滿足了便攜式鏜孔機自動定心要求,極大的降低了工人勞動強度,提高了定心精度和工作效率。
關鍵詞: 在線檢測; 自動定心; 迭代算法
0 引言
便攜式鏜孔機主要應用于大型重工行業,例如: 船舶加工制造業、軍事加工制造業、核電產業等大型難加工,且加工精度要求特別高的行業。鏜孔加工過程中鏜桿軸線的位置決定了加工后孔的位置精度,同時對加工孔的形狀精度也有直接影響。目前國內便攜式鏜孔機的定心方式均采用手動測量、人工估算、手動調整的定心方法,特別是針對有磨損的大型深孔修復時,使用這種調整方法不僅效率低、工人勞動強度大、定位精度差,而且工件加工后易產生廢品,導致巨大浪費; 對于空間位置有限深孔或盲孔,受條件限制工人無法安裝操作時,這就需要運用自動化手段實現鏜孔機自動定心。
因此,開發便攜式鏜孔機的在線檢測自動定心系統是現場加工行業的自動化發展的需求,對現場加工行業的發展有重要的推動作用。
1 、在線檢測自動定心系統
依據現場加工環境,以及系統安裝條件為了實現便攜式鏜孔機的自動定心功能,設計如圖 1 所示的便攜式鏜孔機測控系統圖。
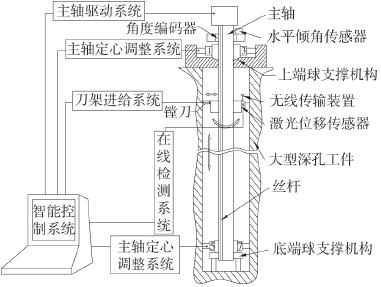
圖 1 大型深孔現場加工機床智能控制系統
該機床的在線檢測系統采用激光位移傳感器的非接觸式測量方式,通過多次測量調整來實現自動定心功能。測控系統主要分為三大模塊: 數據采集模塊、數據處理模塊、運動調整模塊。數據采集模塊: 在選定的測量截面內控制刀架旋轉從而帶動激光位移傳感器圓周運動,完成對工件內腔的圓周掃描,采集得到一組距離數據; 運用無線傳輸技術將這些數據傳輸給上位機,并存儲在上位機中。通過對多個截面的圓周掃描后,得到多組原始數據點,實現對工件內腔原始數據的采集。
數據處理模塊: 上位機對工件內腔原始數據進行合理的運算處理,計算出每個檢測截面的圓心位置,然后通過擬合運算擬合出工件內腔的虛擬軸線; 根據內腔虛擬軸線與鏜桿軸線的空間位置關系,在上( 下) 調整面內計算出虛擬軸線點和鏜桿軸線點的空間位置偏差量。
運動調整模塊: 上位機將空間位置偏差量傳輸給運動控制器,經過運動控制器的運算插補后,將插補信息傳輸給驅動裝置,驅動裝置驅使執行部件運動帶動鏜桿運動,從而實現鏜桿的空間位置調整。
便攜式鏜孔機自動定心過程為: 首先,對進行機械本體各部件進行安裝,然后進行測控系統的安裝,將水平傾角傳感器、激光位移傳感器、角度編碼器和壓力傳感器等檢測元件以及各執行機構的電氣元件同控制系統進行連接,形成一個閉環控制的測控系統。
其次,標定激光位移傳感器發光點距主軸軸心的距離為 r0,獲取一個原始距離值。以水平傾角傳感器檢測方向為標準,標定坐標系方向,并建立 O-XYZ 測量坐標最后,通過激光位移傳感器對工件原始內腔的逐層旋轉掃描如圖 2 所示。
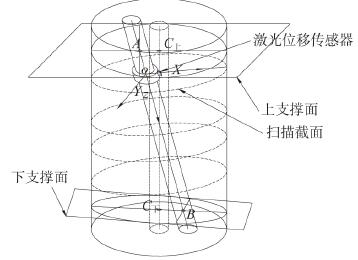
圖 2 工件內腔檢測模型
獲取工件內腔的原始數據; 將得到的每層原始數據運用最小二乘法進行圓形擬合,從而得出每個截面掃描圓的擬合圓圓心及半徑; 然后每個截面處擬合的圓心再通過擬合運算,得出虛擬內腔圓柱的軸線; 在調整截面內計算出兩軸線與截面相交點之間的位置偏移量和,通過數據和與直線度 d 進行判別比較確定是否需要調整,如若需要調整則通過調整機構實現鏜桿自動調整。
經過多次測量、調整后達到定心精度的要求,完成自動定心,然后進行后續加工。2 最小二乘法定心算法根據圖 2 所示,工件內腔輪廓掃描過程中將被測工件內腔沿鏜桿軸線方向劃分為若干個截面,每個截面內在圓周上均分為若干個采樣點,則每個采樣點的極坐標為:
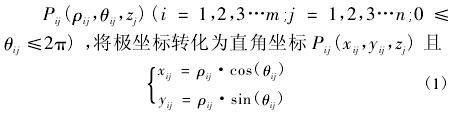
由于工件內腔截面輪廓為非標準圓,取測量截面中第 K 個截面( k≤n) 為研究對象,如圖 3 所示。
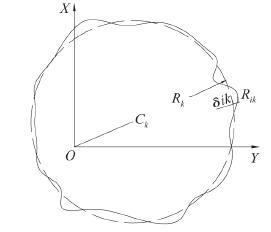
圖 3 第 K 個截面掃描圖
采樣點的位置不可能完全在擬合圓周上,必定會存在誤差,設誤差為 δik。采用最小二乘法擬合圓曲線 ,其原理如下:
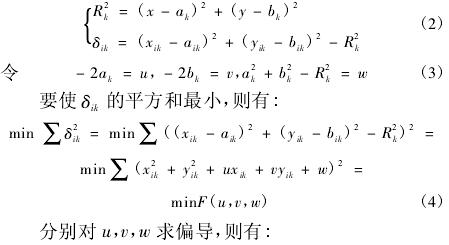
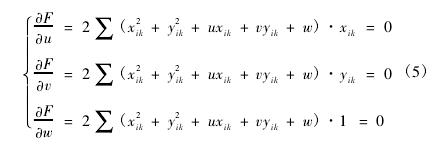
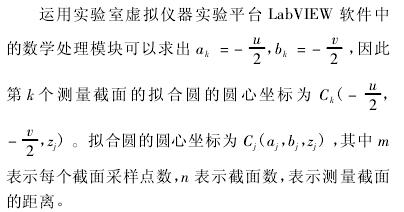
測量 n 個截面可以得到 n 個擬合圓心,將這些擬合圓心值選用最小二乘法進行線性擬合運算,擬合運算后能夠得到一條理想空間直線 C上C下,如圖 4所示。
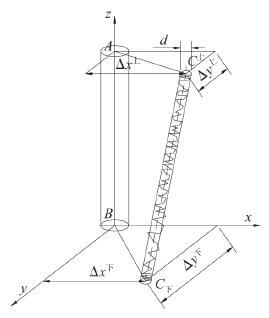
圖 4 自動定心模型
直線 C上C下為鏜桿所要調整目標的位置軸線,鏜桿上下調整面的調整量為 Δx,Δy ,調 整 范 圍 量 為C上C下的直線度誤差 d,根據調整量使鏜桿上下支撐的中心點 A 和點
B 分別與點 C上和點 C下重合,完成一次鏜桿的自動調整。
3 、實驗分析
運用實驗室虛擬儀器實驗平臺 Lab VIEW 軟件,開發測控系統軟件 。根據工件內腔建立實體模型,并進行鏜桿自動定心模擬實驗驗證。工件的原始內腔曲面模型可以自行建立,其母線可為直線,斜線,單葉雙曲線等,其截面可為圓或是橢圓。本文建立的模型為橢圓斜柱模型,其工件內腔各截面 x軸向半徑為 350mm,y 軸向半徑,半徑偏差范圍為,截面個數為,截距為,相對水平面 x 軸向偏角 α = 10°,y 軸向偏角,生成工件內腔原始數據。
并通過原始數據進行多次迭代自動調整模擬,調整過程及結果如圖5、圖 6 所示:
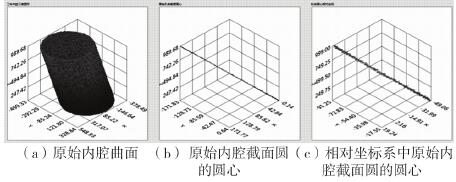
圖 5 未調整時原始內腔的三維信息圖
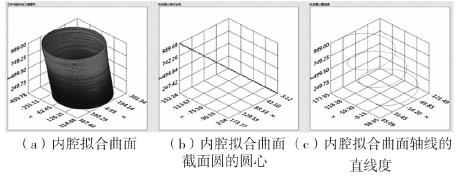
圖 6 未調整時擬合內腔的三維信息圖
經過三次迭代運算、調整后的圖形如圖 7 和圖 8所示
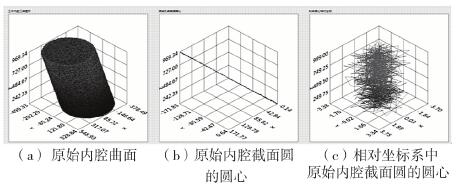
圖 7 三次迭代調整后原始內腔的三維信息圖
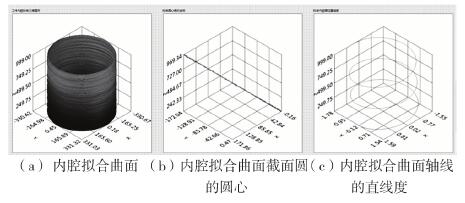
圖 8 三次迭代調整后擬合內腔的三維信息圖
以建立橢圓斜柱工件內腔模型時的坐標系為絕對坐標系,檢測裝置在工件內腔內部,沿鏜桿方向運動,對工件內腔進行圓周掃描測量從而獲得的的原始曲面如圖 5a,對原始內腔圓的圓心在絕對坐標下顯示如圖5b,將原始內腔截面圓的圓心轉化為在以鏜桿為 Z 軸的相對坐標系下的坐標如圖 5c。對原始曲面進行擬合得到內腔擬合曲面如圖 6a,把圖 6a 中擬合曲面圓的圓心在絕對坐標系中顯示如圖 6b,將圖 6b 中一系列的圓心進行運算,便可得到內腔擬合曲面的圓柱直線度如圖6c。
經過合理的處理獲得上下端的調整量,根據調整量對鏜桿進行模擬調整,一次調整完成后再次進行數據采集、模擬運算然后進行調整。經過三次迭代運算、調整后得到圖 7 和圖 8 分別對應于圖 5 和圖 6。為了實現從原始內腔曲面模型的建立到自動運行調整完成的過程中,對測量數據和調整結果進行記錄和保存,最終生成檢測報告,以便于輸出和打。自動檢測定心軟件可以自動形成表 1,如下所示。
表 1 自動定心實驗數據

以上實驗數據和調整的圖形中可以看出,該自動定心系統用于定心時,經過第三次迭代調整后,能夠得到很好的定心效果。定心偏差結果如下:
角度偏差:

上端偏差為:
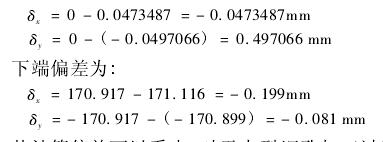
從計算偏差可以看出,對于大型深孔加工過程中通過虛擬軟件控制調整,說明該自動定心系統能夠很好的實現自動定心要求,并且定心誤差能達到 μm 級,實現現場加工設備的高精度檢測和精確定位。
4 、結論
綜上所述,本文采用互為基準的方法,對便攜式鏜孔機的自動定心測控系統進行了設計,并通過實驗驗證,結果表明:
( 1) 該系統能夠實現在線檢測,快速進行數據處理,定心精度高,系統穩定,操作方便。
( 2) 該系統具有多用性,不僅能用于加工前的系統自動定心,還能夠用于加工后被加工工件的質量檢測,可以實現定位檢測和加工質量檢測一體化。
( 3) 運用自動化系統,大大降低了操作人員的勞動強度,提高了工作效率,提升了安全性能。同時也提高了現場加工機械的自動化程度,為其他機械自動化的發展提供了參考。
投稿箱:
如果您有機床行業、企業相關新聞稿件發表,或進行資訊合作,歡迎聯系本網編輯部, 郵箱:skjcsc@vip.sina.com
如果您有機床行業、企業相關新聞稿件發表,或進行資訊合作,歡迎聯系本網編輯部, 郵箱:skjcsc@vip.sina.com