基于嵌入式PLC的數控機床自動控制系統
2020-11-2 來源:陜西機電職業技術學院 智能制造學院 作者:孫釗
摘 要:隨著科技不斷進步,PLC控制器在數控機床得到了廣泛地應用。以控制器框架結構為基礎,研究數控機床的自動控制系統,計算并比較系統內重要的運行參數,并結合硬件結構的不同屬性,對嵌入式 PLC系統方案進行分類。研究結果顯示,PLC自動化控制系統具有較高的抗干擾能力,可提高系統運行的準確性和穩定性;滾動軸的導程由電機運轉速度和移動桿的轉動速度決定,當電機運轉速度越高時,導程的數值越小,反之則越大。研究結果為數控機床自動控制系統性能提升提供了科學依據。
關鍵詞:PLC;數控機床;自動化;控制系統
0、引言
現在工業的自動化、集成化以及柔性化是提高勞動生產率、提升產品質量的基礎。而隨著科技的不斷進步,使 得 數控機床的 控 制 電 路 由 傳 統 的 繼 電 器 邏 輯 電 路 RLC(RelayLogic Circuit-RLC)逐 步 升 級 為 可 編 程 邏 輯 的 控 制 器 PLC(Programmable Logic Controller-PLC),其 PLC 控制系統的發展是以傳統的繼電器、接觸器控制為基礎,采用特殊的存儲介質,為特殊的用途而設計出來,主要實現內部介質存儲、運算過程分析、程序結構控制等功能,控制各種類型的機械或生產過程,其在數控機床中常以內裝式和獨立式兩種形式存在。在機械 行 業 的 應 用 過 程 中,可 以 大 大 的 節 省 人 力 勞動,提高工業生產效率,因其邏輯編程操作簡易,具有較高的抗干擾能力,提高了系統運行的準確性和穩定性。本文就針對于在 PLC的基礎之上研究數控機床的自動控制系統的設計。可編程邏輯控制器是一種以微處理器為基礎的數字運算電子系統,該系統在數控機床自動化控制中的應用,使得整個系統的運行穩定性和有效性大大提高。PLC 是一種可編程控制器件,其存儲器類型屬于可編程存儲器,完成系統指令下達、數據邏輯運算、計算順序控制等功能,通過數字式的信息處理方式實現輸入輸出方式對相關機械的自動化生產控制。該控制器屬于新型的工業控制器,既能控制開關量,也能控制模擬量,也可以將計算機與自動化控制技術相結合,同時利用大量的集成電路技術,大大的提高整個系統運行時的抗干擾性,使得系統持續不斷的工作,從而提高生產效率,PLC集成體積小,編程簡單,適應性強等特點,使得 PLC在機械工業中的使 用 范 圍 越 來 越 廣,同 時 對 復 雜 的系統進行綜合梳理并對系統實現控制。
1、PLC數控系統
1.1、PLC硬件框架
PLC數控系統相較于傳統的計算系統具有對周圍環境適應性強、程 序 語 言 識 別 速 度 快 和 系 統 編 程 穩 定 性 好 等 特點,同時 PLC數控系統在實 際 的 生 產 過 程 中 對 硬 件 接 口 具有較高的適應性。因此,對于數據控制單元由系統內的硬件組成和用戶使用環境構建,二者相互聯系,組成了 PLC 數控系統的基礎單元結構,如圖1所示。
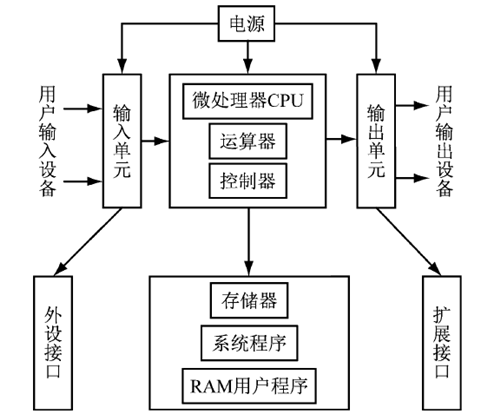
圖1 PLC硬件組成框架
PLC硬件組成框架主要由內設接口和外部接口兩大部分構成,其中內設接口包括用戶輸入單元、用戶輸出單元、微處理器 CPU、運算器和控制器,當輸入單元和控制單元接通電源后,輸入單元采集用戶的設備的基本信息,以電信號的形式傳輸到控制單元,經過微處理器 CPU 對接收信號分析和運算器綜合計算,以數字信號的形式傳輸到控制單元,對傳輸信號進行編碼解析,最后輸出至用戶設備;系統內的輸入單元對應外設接口,輸出單元對應擴展接口,同時,在外設單元中還包含存儲器、系統程序、RAM 用戶 程 序。以上單元接口在系統程序的控制下,可以將用戶的信息進行及時存儲,在運算的過程中對程序的正確性對照檢查,保障內部構件的準確性和完整性,最后將運算的程序存儲于系統的結構單元,并將用戶的信息在存儲設備識別并讀取,通過編譯器將程序信號轉化為數 據 信 號,以 此 實 現 PLC 數 控 系 統 的全部功能。
1.2、數控系統構成
數字控制(Numerical Control)對于以數字化的信號對機床的運行和使用實現控制。其數控機床的主要構成部分由程序介質、數控裝置、伺服系統以及機床主體四部分組成,如圖2所示。
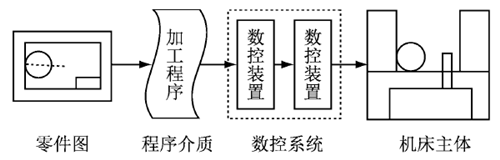
圖2 數控機床的組成
加工編碼是將零件加工程序使用相應的格式和代碼存儲在一種程序載體上,同不同類別數控機床進行對比,將這些程序 信 息 輸 入 到 CNC(Computer Numerical Control)單元。數控系統包括數控裝置和伺服系統。其中數控機床的主要組成部分是主控裝置,采用多個微處理器的 CNC 裝置,根據輸入數據,對所有需要輸出的零部件采用編碼處理;伺服系統是 PLC系統中處 于 核 心 位 置,實 現 數 控 機 床 的 進給伺服控制和主軸伺服控制。機床主體就是為了加工零件,是數控機床的主要部分,包括機體、主軸箱、刀架等機件。其作用是處理各 種 原 材 料,按 照 預 設 的 零 件 構 圖 進 行 加 工 設計。在實際的數控機床運行過程中,很有可能會發生緊急突發的狀況,操作人員的失誤可能導致整個生產的失誤。在數控機床的自動控制系統中,為了避免突發事件,會增加圖書的設計結構,比如緊急按鈕和導程等部件。
2、系統參數計算
機床運動參數計算是系統正常運行的保障,針對機床的參數計算需要掌握其重要的部件,機床中的滾動軸是正常穩定運轉不可或缺的部分,常規滾動軸的軸心分別朝向固定面板的兩端,從而確保運行平穩,PLC 系統的機床涉及的參數種類多,需要對重要的參數進行計算并比較,為機床及時檢修提供數據支撐。
機床滾動軸的重要指標是導程,在機床設計過程中根據接觸表面的光滑程度來制定適合的機床部件,例如結合材料力學選取符合要求的物理參數,將參數類型進行歸整,作為PLC的數控機床生產的重要指標。滾動軸的導程由電機運轉速度和移 動 桿 的 轉 動 速 度 決 定,當 電 機 運 轉 速 度 越 高時,導程的數值越小;當機床移動桿的轉動速度越大時,導程的數值越小。滾動軸導程的計算公式如式(1)。
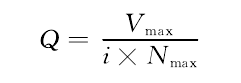
式中:Nmax為電機運轉速度,單位為 m/s;Vmax為移動桿轉動速度,單位為 m/s;i為傳動比,這里取值為1;Q 為滾動軸的導程。
數控機床滾動軸不同的安裝方法,其在接觸面的受力也不盡相同,結合機床構造和工程力學,最小安裝直徑受電動機的運轉速度、使用材料的伸縮程度、轉動桿的承受荷載和固定端到自由端的距離決定的,其計算公式如式(2)。
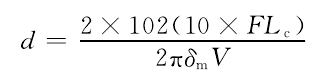
式中:V 為電動機的運轉速度,單位為 m/s;δm為材料的伸縮程度;F 為轉動桿 的 承 受 荷 載,單 位 為 N;LC為 固 定 端 到 自由端的距離,單位為 m。
數控機床在運行過程中,需要對其運行荷載 進 行 計 算。如果接觸面的承受荷載遠大于它的運行荷載時,就會出現不平穩運行,甚 至 產 生 安 全 事 故。因此計算數控的運行荷載非常重要,該荷載主要由轉動軸的穩定系數、材料的彈性模量、移動桿的慣性矩、轉動軸的移動距離決定,數控機床運行荷載的計算公式如式(3)。

式中:PK為 運 行 荷 載,單 位 為 N;FK為 轉 動 軸 的 穩 定 系 數(雙軸時為2,單軸時為1);E 為材料的彈性模量,單位為 Pa;I為移動桿的慣性矩,單位為 m2;L 為轉動軸的移動距離,單位為 m。
3、嵌入式PLC控制系統
嵌入式 PLC系統 的 內 部 硬 件 結 構 有 著 較 大 的 差 別,結合硬件結構的不同屬性,嵌 入 式 PLC 系 統 按 照 組 成 結 構 不同可分為:傳統 PLC控制方案、內置控制器運行方案和計算機通信接口控制方案,根據方法和過程不同控制方案如下:
(1)傳統 PLC控制方案
傳統 PLC控制方 案 中 是 以 計 算 機 為 基 礎,將 運 算 程 序以系統的組成部分為單元,固定在系統的硬件結構中,如圖3所示。

圖3 傳統 PLC系統結構框架
PLC運行系統與 PLC開發系統以信號交互形成通信體系,結合系統的使用要求對在計算機平臺編寫的程序代碼,以數據信號的形式傳輸到下一個接口處,并實現系統數據控制和程序運行。
(2)內置控制器運行方案
內置控制器是 PLC 系 統 獨 立 的 組 成 部 分,該 系 統 的 重要組成部分為微型處理器,主要實現在指定系統中完成信號接收、數據分析及代碼編譯,以系統硬件組成的方式嵌入在系統結構中,實現控制系統信號交互及數據通信等功能,如圖4所示。

圖4 內置控制器結構框架
在 PLC運行系統中嵌入式控制器與 PLC開發系統實現數據通信功能,根據開發系統和運行系統分析,在標準的通信協議下完成交互信號與運行系統和數據接口準確對接,實現數據信號實時交互。
(3)計算機通信接口控制方案
在計算機通信接口控制系統的硬件部分主要由控制計算機、系統總線 接 口 和I/O 接 口 組 成。PLC 開發系統和運行系統根據網絡I/O 接口 進 行 數 據 交 互,同 時 PLC 運 行系統與I/O 接口和系統總線接口實現信號傳遞,以上結構單元組建控制計算機與網絡接口完成信號控制。計算機通信接口框架結構,如圖5所示。
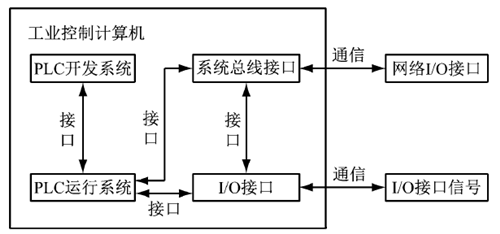
圖5 計算機通信接口結構框架
4、基于PLC的控制系統設計
4.1、基本功能
PLC技術相對于傳統的控制技術擁有特殊的功能,在系統組成部分擁有多項的基本功能,其基本功能如下。
1)PLC技術以強化邏輯運算功能為目標,功能介于中心主要數據控制和配電裝置核心功能相互轉化;
2)有專一的存儲用戶程序的存儲器,對復雜的控制對象以及控制邏輯更靈活,其用戶程序采用的邏輯順序關系和傳統的繼電器電路十分相似的梯形圖形編輯;
3)PLC可以和多種外部的設備進行連接,更方便的實現程序的顯示、編輯等功能;
4)PLC具有較高的抗干擾能力,體積小,摒棄了傳統繼電器的接觸不良、磨損等特點;
PLC技術 在 實 際 的 生 產 中 起 到 了 重 大 的 作 用。采 用PLC的數控機床機構更加緊湊,功能更加豐富,在自動化程度較高的生產制造系統和加工設備中,PLC是一種不可或缺的控制裝置。
4.2、PLC控制系統組成
PLC采用典型的計算機結構,由 CPU、輸入、輸出接口電路、讀寫存儲器等,該系統可以看成由變量的信號輸入和信號輸出變量組成,此時的 PLC 相當于一個中間處理器,將輸入的 變 量 經 過 一 定 的 編 程 程 序 的 處 理 以 得 到 輸 出 變量。其控制結構圖,如圖6所示。
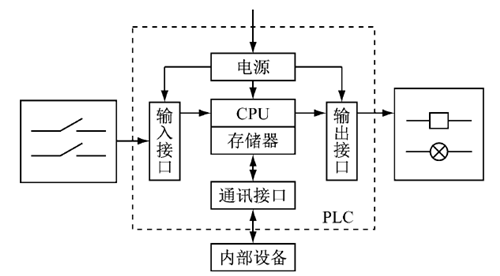
圖6 PLC系統基本功能框架圖
輸入部分 此 部 分 的 輸 入 端 子 與 按 鈕 開 關、液 位 報 警 開關、壓力檢測開關等連接,主要用來收集系統中的各種實際數據,以重復掃描的方式進行用戶程序的執行,并按照程序事先編寫好的地址將輸入信號讀入輸入映像寄存器中并執行,程序執行過程中,以掃描周期為周期進行獲取輸入數據。控制部分此部分按照被控對象的實際控制要求所編寫的用戶程序進行反復執行,并按照順序進行掃描執行,并將執行結果寫入有關輸出映像的寄存器中。輸出部分該部分的輸出端子與接觸器、三色警報、驅動使能等連接,是電路的輸出狀態,用于控制被控制對象的動作操作。根據所設計需要的輸出模式,完成指定的操作,并將輸出映像寄存器中的狀態轉移到輸出鎖存寄存器中,實現外部負載。
4.3、PLC模塊化設計
本次設計中,將 PLC模塊劃分為5個模塊,公共信號模塊、基本控制 模 塊、刀 架 模 塊、主 軸 模 塊 和 報 警 模 塊。其中公共信號模塊的主要作用是將 PLC 和 NC 之間的信號進行相應的處理;基本控制模塊的主要作用是程序的啟停、緊急處理等;刀架模塊主要是實現選擇合適的刀架、以及對刀架的定位等邏 輯 控 制 功 能;主 軸 模 塊 主 要 是 對 主 軸 的 正 反轉、主軸定位等進行控制,并通過 PLC 的編程實現參數的修改等;警報模塊主要是機床的故障、人為誤操作等進行檢測并同時給以反饋警報信息等。該模塊的功能實現可以通過一個主程序以及若干的子程序一起完成,實現對機床的各種控制作用,其主要的子程序結構,如表1所示。
數控機床中 PLC 技術 的 實 現 的 基 礎 就 是 程 序 指 令,相應的指令會將信號和程序納入控制體系中。PLC 技術的運用,可以實現整個控制系統的升級以及改進,在實際的運行過程中實現高效率的數控機床控制,并對該系統結構進行不斷地優化,從而升級數控機床的控制性能。
表1 主要子程序庫結構
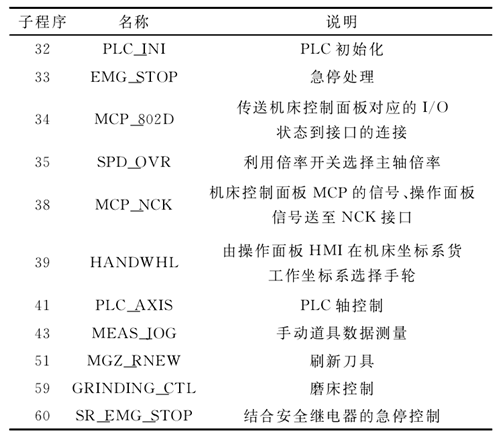
5、總結
在我國經濟和社會的快速發展中,對數控機床的需求不斷的提高,而 PLC在數控機床中的應用,不僅大大的提高了整個系統的生產效率,而且有效的實現數控機床的自動化控制,對提高企業的經濟效益有很大的益處。結合當今數控系統的特點,要不斷地改善 PLC的功能,特別是完善和改善上位機軟件的功能,以及對數控系統編程語言的進一步統一,這些問題的解決,會使得我國數控系統性能得到很大的提升。
投稿箱:
如果您有機床行業、企業相關新聞稿件發表,或進行資訊合作,歡迎聯系本網編輯部, 郵箱:skjcsc@vip.sina.com
如果您有機床行業、企業相關新聞稿件發表,或進行資訊合作,歡迎聯系本網編輯部, 郵箱:skjcsc@vip.sina.com
更多相關信息