激光切割技術在太陽能裝備生產中的精度優化
2025-4-18 來源:內蒙古訊馳科技有限公司 作者:岳 雷
【摘要】: 隨著全球對可再生能源需求的持續增長,提高太陽能電池板的生產質量與效率成為行業迫切需要解決的問題。文章旨在通過采用高精度激光切割技術,實現電池片的高效、精準加工,從而減少微裂紋產生,提高電池板的整體性能和產出率。研究方法包括激光設備的選擇與配置、激光切割參數的優化、電池片切割精度的控制技術、自動化與集成系統的應用。通過對比分析優化前后的生產數據,評估激光切割技術的實際效益。
【關鍵詞】: 激光切割技術 ; 太陽能裝備生產 ;半片單晶硅太陽能電池板 ; 精度優化
在太陽能裝備生產中,激光切割技術的應用為精度優化提供支持,在高性能單晶硅太陽能電池板的生產過程中,該技術不僅能提升制造效率,同時也有助于提高產品的性能和可靠性。通過精細控制激光的功率、波長、脈沖寬度及聚焦精度,
可以有效減少硅材料的熱影響區,降低微裂紋的生成率,從而顯著提升電池板的光電轉換效率。
1. 生產背景
近年來,隨著全球對可再生能源需求的快速增長,內蒙古訊馳科技有限公司計劃擴大生產規模,提升產品的競爭力,并計劃通過采用先進的激光切割技術,提升半片單晶硅太陽能電池板的生產精度和效率。引入高精度激光切割技術,預期將電池片的微裂紋率降低 30%,從而顯著提高最終產品的轉換效率和可靠性,同時引入自動化激光切割系統,預計生產線的總體效率將提高 25%,同時減少人工操作所導的誤差和物料浪費。
2. 理論分析
2.1 激光切割技術的原理
激光切割技術能夠產生極窄的熱影響區(Heat-Affected Zone,HAZ),減少材料的熱變形,確保加工精度。激光切割設備主要由激光發生器、光束傳輸系統、工作臺及數控系統組成,其中激光發生器是產生激光光源的核心部件,光束傳輸系統則負責將激光引導至材料表面。通過精確控制激光的功率、波長、脈沖頻率和聚焦精度,可以對硅片進行高精度的切割與雕刻。激光切割操作展示如圖 1 所示。
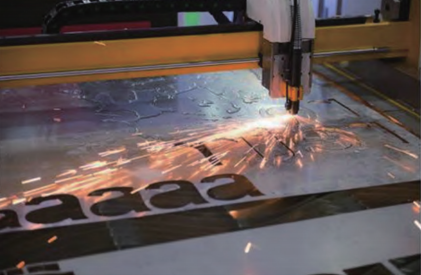
圖 1 激光切割操作展示
在激光切割過程中,激光光束高度集中的能量被材料吸收后迅速轉化為熱能,使得材料局部溫度急劇升高至蒸發點,從而使材料在極短時間內蒸發形成切口。
2.2 材料選擇與激光參數的關系
針對多晶硅與單晶硅兩種太陽能電池板材料展開激光切割實驗,實驗中設置了多組激光參數,包括激光功率、脈沖頻率、波長和聚焦光斑,以觀察這些變量如何影響切割質量和效率。采用固體激光器——Nd 激光器,波長固定為 1064nm,
材料選為標準尺寸(100mm×100mm×1mm)的單晶硅和多晶硅樣品。激光參數設置 : ①功率調節范圍:100~600W ;②脈沖頻率 :200~1000Hz ;③聚焦光斑直徑 :0.1~1mm。
實驗期間,每種材料在不同的激光參數下進行切割,每個設置重復 3 次以確保數據的可靠性,使用高速攝像機記錄切割過程,期間重點關注熱影響區和邊緣質量,切割后,使用顯微鏡和表面粗糙度儀評估每個樣品的邊緣平滑度和微裂紋。在實驗過程中發現,單晶硅和多晶硅對激光功率的反應不同,多晶硅在較低功率下即可達到良好的切割效果,而單晶硅則需要較高功率。同時聚焦光斑對切割質量有顯著影響,過大或過小的光斑會增加熱影響區,影響切割質量。實驗結果見
表 1。
表 1 激光切割實驗結果
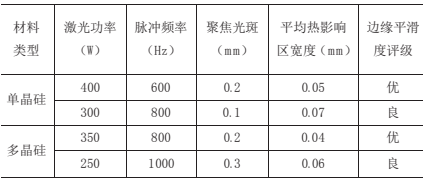
從結果來看,激光參數的優化對于提高太陽能電池片的切割質量至關重要。通過精確控制激光功率、脈沖頻率和聚焦光斑直徑,可以顯著減少熱影響區,提高切割精度。
3. 基于激光切割技術的太陽能電池板生產精度優化
3.1 激光設備選擇與配置
激光類型是決定設備選擇的首要因素。在太陽能電池板的生產中,Nd 激光器提供了適合硅材料切割的波長(1064nm)。同時還采用了光纖激光器,該設備適用于高速切割和自動化生產,保證了切割過程中光斑的高聚焦性和切割精度。
激光功率是影響切割能力和速度的重要參數,太陽能電池片切割通常需要的激光功率范圍為200~500W,根據生產規模和切割厚度的不同,選擇合適的激光功率至關重要。
激光設備的配置還需要考慮脈沖寬度和重復頻率,脈沖寬度通常在納秒到微秒級別,而重復頻率可以影響切割過程的熱積累,進而影響切割質量。較短的脈沖寬度和適當的重復頻率有助于減少熱影響區,提高切割精度。兩種激光設備及配置見表 2。
表 2 激光設備選擇與配置
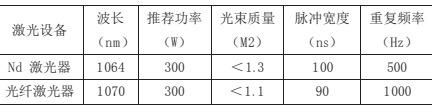
3.2 激光切割參數優化
切割參數的優化需要精確調整激光功率、脈沖寬度、重復頻率和聚焦精度等參數,以適應不同材料的特性并最大化切割效率。為了確保參數優化的有效性,需要探索更理想的切割參數。激光類型采用光纖激光器,波長固定在 1070nm,材料選擇 0.5mm 厚的單晶硅電池片,主要的測試參數為激光功率、脈沖寬度、重復頻率。
常規工業標準參數下,激光功率為 300W,脈沖寬度 100ns,重復頻率 500Hz。這些參數在先前的生產批次中提供了相對理想的切割效果,但伴隨有較寬的熱影響區和一定的微裂紋生成。在參數優化過程中,將激光功率逐步調整至更細致的范圍,如 280~320W,脈沖寬度減少至 80ns以減少熱效應,同時增加重復頻率至 1000Hz 以提高切割速度和減少熱累積。通過優化,熱影響區顯著減少,從原來的平均 0.2mm 降低至0.1mm,同時微裂紋的發生頻率也由原來的每10cm 一個減少至每 50cm 才出現一個。
3.3 自動化與集成系統的應用
集成高級自動化技術,使得激光切割的精確率與效率進一步提升,這些系統包括高精度機械定位系統、實時監控軟件以及自動負載和卸載機制。這些技術的綜合應用顯著提高了生產線的運行效率和產品質量。太陽能電池板自動化激光切割如圖 2 所示。
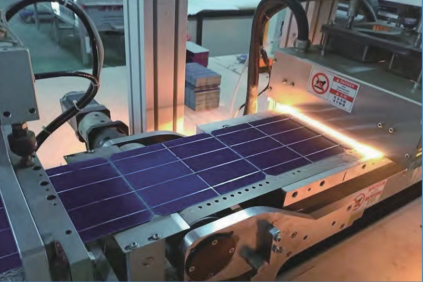
圖 2 太陽能電池板自動化激光切割
首先, 機械定位系統采用精度高達±0.01mm 的伺服電機和線性導軌,確保激光切割頭沿預設路徑精確移動。集成的視覺識別系統可以實時檢測電池片的位置和方向,自動校正切割路徑,減少人為誤差。生產線上,通過實施這
些自動化技術,電池片的定位偏差已從之前的0.5mm 降低至 0.1mm。
其次,實時監控軟件能夠實時收集切割過程中的數據,如切割速度、激光功率和聚焦精度,并根據實時反饋調整操作參數。在自動化系統中,所有操作參數都可以在中央控制室內進行監控和調整,從而確保切割過程達到最優狀態。
4. 生產成效評估
為了全面評估生產成效,設定了多個關鍵性能指標(KPIs),包括生產速度、產品合格率、廢品率以及生產成本。這些指標的數據收集涵蓋了技術實施前后的廣泛對比,確保了評估的準確性和科學性。指標評估中,采用對比分析法,通過收集激光切割技術實施前后的生產數據,對比分析其性能指標的變化。數據收集主要依賴于生產線的自動記錄系統和質量控制部門的報告。在激光技術實施前后,連續 3 個月內的生產數據被記錄和分析。這包括每月的生產總量、廢品數量、平均生產速度以及生產成本。激光切割技術優化前后的生產數據對比見表 3。
表 3 激光切割技術優化前后的生產數據對比
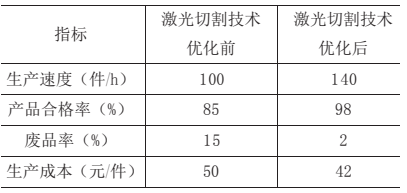
從對比結果來看,引入激光切割技術后,生產速度顯著提升,每小時生產件數從 100 件提高到 140 件,增加了 40%。產品合格率也從 85% 提高到了 98%,廢品率大幅降低了 86.7%,從 15%降到了 2%。這一顯著的質量提升歸因于激光切割的高精度和重復性。生產成本每件從 50 元降至42 元,降低了 16%,這主要得益于廢品率的大幅降低和生產效率的提高。
5. 結束語
激光切割技術在太陽能裝備生產中的應用顯著提升了制造精度和生產效率,不僅提高了生產速度和產品合格率,同時顯著降低了廢品率和生產成本。這些成效得益于激光切割的高精度、快速響應和重復性能,使得生產過程中的每一步都更加精確和可控。同時生產線的自動化和集成系統的優化,進一步增強了整個生產過程的協調性和流暢性,降低了人力成本,提高了操作的安全性和便捷性。
投稿箱:
如果您有機床行業、企業相關新聞稿件發表,或進行資訊合作,歡迎聯系本網編輯部, 郵箱:skjcsc@vip.sina.com
如果您有機床行業、企業相關新聞稿件發表,或進行資訊合作,歡迎聯系本網編輯部, 郵箱:skjcsc@vip.sina.com