一種磨床液壓主軸懸臂結構熱變形抑制措施
2019-5-30 來源:中國第一汽車股份有限公司技術中心 作者:王勛 徐婉竹 劉瑤 董樂 王樂
摘要】薄環狀零件越來越多地應用于發動機密封裝置,針對薄環狀不銹鋼密封件的平面磨削工藝進行了試驗研究。磨削過程中,液壓懸浮主軸高速旋轉與高黏度液壓油摩擦發熱,溫升使得支撐主軸懸臂膨脹變形,導致薄環狀零件尺寸加工精度降低。試驗驗證一種磨床液壓主軸懸臂結構熱變形的抑制措施,即降低液壓油黏度,提高其導熱性,降低主軸懸臂結構變形量及熱穩定時間,提高零部件的加工精度和加工效率。
【關鍵詞】磨床 主軸熱變形 低黏度液壓油
一、前言
新型高效汽車發動機技術的研發和應用,在國內汽車產業自主新產品開發中發揮了重要作用。為了實現高溫、高壓工作狀態下發動機缸體的有效防漏(油、氣)和工作時間延長,越來越多的具有優異的機械加工性能和穩定的熱化學耐蝕性的不銹鋼環形薄型零件應用于新型發動機密封裝置。然而傳統的車削加工方法由于積屑瘤的產生以及刀具進給痕跡殘留于已加工表面,很難得到高質量的加工表面及高等級尺寸精度。與此同時,環形薄型零件具有低剛度特性,傳統的車削加工不易裝夾并會造成車削過程中工件切削深度方向的加工精度降低。高精度液壓主軸磨削加工方法在加工效率和加工精度方面較車削加工具有明顯優勢,越來越多地應用于汽車發動機高精度關鍵零部件的成形加工。然而液壓懸浮主軸高速旋轉與承載液壓油摩擦發熱,導致液壓油溫度升高,使得機床支撐主軸用懸臂結構溫升變形,造成高精度磨床主軸在多次停機時重復定位精度降低,或需在再次開機時消耗較長時間達到機床主軸的熱穩定,降低零部件的尺寸加工精度及加工效率。
二、試驗裝置及檢測方法
1. 試驗裝置
試驗用薄環狀工件的毛坯料為經過熱處理工藝的301不銹鋼料。進行精密磨削前,需通普通磨削方式制備精密磨削工藝用裝夾基準面。最終精磨過程的試驗裝置如圖1所示。
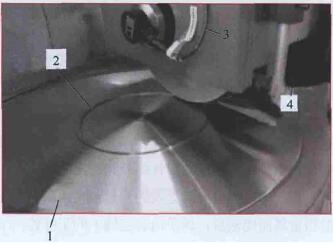
圖1 試驗裝置
1.旋轉工作臺 2.薄環工件 3.磨頭 4.磨削主軸懸臂機構
為降低磨削過程中工作臺熱量的產生導致工件熱變形,工作臺采用條狀電永磁吸盤作為與工件的吸附面。電永磁吸盤不僅可以提高工件的裝夾速度和裝夾精度,而且具有強勁、實用和高效等特點。本文中所使用的支撐磨床主軸用的懸臂結構如圖2所示。
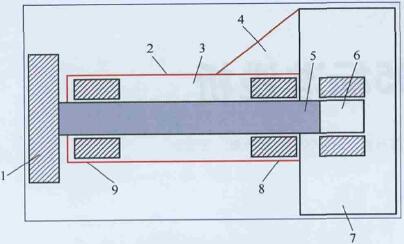
圖2 磨削主軸懸臂結構示意圖
1.磨頭 2.支撐主軸用懸臂結構 3.主軸液壓油 4.連接加固法蘭5.磨削主軸 6.力矩電動機
7.磨削軸承載基體 8、9.動壓軸承
該磨削主軸采用動壓支撐方式,且工作時處于高速運動狀態,主軸表面與液壓油摩擦生熱導致液壓油區域溫度升高。由于該懸臂結構尺度較長,很容易造成懸臂結構的熱變形。當主軸液壓油區域溫升與周圍環境熱交換達到穩定時,主軸懸臂結構變形量達到穩定狀態。
2. 檢測方法
如圖3所示為檢測主軸懸臂結構變形量示意圖,將千分表(Mitutoyo, 1109S-10, 位置分辨能力1μm)固定于懸臂結構與磨頭的連接處,隨后使液壓主軸處于工作狀態,轉速為3 600r/min
。將磨床工作臺處于靜止狀態,其上表面作為檢測基準面,測量懸臂結構相對于磨床工作臺的位置相對變化量。該相對變化量直接影響被磨削工件的磨削去除量深度值,從而影響零部件磨削加
工后的尺寸精度。由于磨削過程中液壓油的摩擦發熱,使得本研究使用的磨床主軸懸臂相對于工作臺位置距離增大。
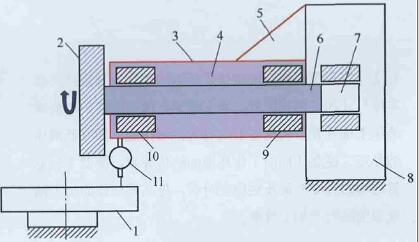
圖3 主軸懸臂結構變形量檢測方法
1. 工作臺 2.磨頭 3.支撐主軸用懸臂結構 4. 主軸液壓油5.連接加固法蘭 6.磨削主軸
7.力矩電動機 8.磨削軸承載基體9、10.動壓軸承 11.千分表
主軸懸臂結構變形量檢測結果及其達到熱交換穩定狀態所需的時間如圖4所示,為保證試驗數據的可重復性,本試驗進行了兩次試驗數據的檢測提取,兩次試驗的結果相互吻合,主軸懸臂結構的熱變形量為60 μm及熱穩定時間約為200 min。

圖4 主軸懸臂結構變形量及其達到穩定狀態所需時間
三、液壓主軸懸臂結構熱變形抑制措施
為了降低高速磨削主軸與液壓油間的摩擦生熱,可降低液壓油黏度,以減小主軸與液壓油接觸面之間的摩擦因數以降低產熱率,并且增大相互接觸面之間的導熱率,降低熱平衡所需時間。目前該磨床使用的主軸液壓油為工業用美孚10號主軸油,其40℃時的運動黏度為10mm2/s。為了驗證低黏度液壓油在降低主軸摩擦生熱方面的有效性,目前本研究選用體積膨脹系數小、比熱容大、具有良好的黏溫特性的低黏度2號主軸液壓油,其40℃時的運動黏度為2.1 mm2/s,其密度基本與純水相同。為了驗證本文所提出的降低磨削主軸摩擦生熱措施的工業實用性,將降低運動黏度的主軸液壓油裝載于發動機薄環件精密磨床,檢測主軸懸臂的熱變形量及熱平衡所需的時間,如圖5所示。
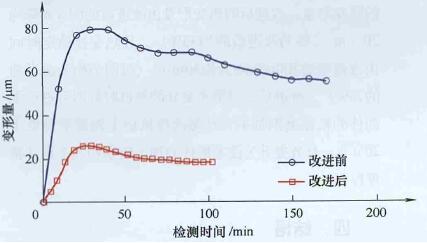
圖5 液壓油改進前后主軸懸臂變形量及其達到穩定狀態所需時間
基于本文提出的降低液壓主軸液壓油運動黏度的措施以降低主軸摩擦生熱的措施可有效降低主軸懸臂的熱變形量,改進后的熱變形量由改進前的60μm降為20μ m (降為改進前的約33%),且熱交換穩定時間由改進前的200min降為約50min (時間節約為改進前的75%)。改進后,只需不足1h的熱機時間即可進行零部件的精密磨削加工,且每次停機后主軸變形量低于20μm,有效提升關鍵零部件的加工效率和加工尺寸精度控制。
四、結語
本研究針對薄環狀工件的平面精密磨削尺寸精度提升進行了試驗研究。磨削過程中,液壓懸浮主軸高速旋轉與高黏度液壓油摩擦發熱,使得支撐主軸懸臂溫度升高、與工作臺相對磨削位置熱膨脹變化,導致薄環狀零件尺寸加工精度降低。本文提出并試驗驗證一種磨床液壓主軸懸臂結構熱變形的有效抑制措施,即降低液壓油黏度,提高其周圍工作環境的熱傳導率,降低主軸懸臂結構的熱變形量及熱穩定時間,提高零部件的加工精度和實際生產加工效率。
投稿箱:
如果您有機床行業、企業相關新聞稿件發表,或進行資訊合作,歡迎聯系本網編輯部, 郵箱:skjcsc@vip.sina.com
如果您有機床行業、企業相關新聞稿件發表,或進行資訊合作,歡迎聯系本網編輯部, 郵箱:skjcsc@vip.sina.com
更多相關信息