小型齒輪加工單元自動上下料系統的設計與實現
2019-11-13 來源:南京工業大學機械與動力工程學院等 作者:陸 寧 洪榮晶 謝 杰
采用機械手實現自動上下料技術是機器人技術應用的一個重要方面。機器人自動上下料系統具有定位精度高、無疲勞作業、結構簡單、便于維護等優點,因此廣泛應用于各制造領域。
在小型齒輪加工過程中,大多數中小企業仍采用人工或半自動作業,齒輪的上下料需要重復持續作業,工人勞動強度較大,持續作業的一致性與精準性得不到保證而導致的齒輪質量不合格問題也時有發生。隨著用工成本的提高及生產效率提升帶來的競爭壓力,加工能力的自動化程度及柔性制造能力成為企業競爭力提升的關鍵。
本文以某企業實際生產需求為研究背景,從改進小型齒輪加工過程中人工上下料存在的不足出發,設計了一套小型齒輪加工單元自動上下料系統。系統以S7-1500PLC 為主控制器,綜合運用了工業機器人技術、工業以太網技術及傳感器技術等,有效的實現了齒輪加工過程中的自動上下料工作。降低了工人勞動強度,保證了產品加工質量,實現了小型齒輪的大批量、自動化生產。
1、系統方案提出
1. 1 系統組成、布局確定
此項目要求機器人上下料工件為小型齒輪,如圖1 所示。工件包括兩道加工工序: 端面及外圓車削和輪齒加工。
由工件加工工藝分析擬定采用數控車床對齒輪的端面及外圓進行車削。考慮到齒輪整體加工精度要求不高,且需要大批量加工,故選取滾齒的加工工藝。在合理計算、規劃機床加工時間與機器人上下料時間的前提下,本項目采用一臺工業機器人為一臺數控車床及一臺數控滾齒機上下料的方案,輔以工件翻轉臺、工件儲料架等周邊設備,搭建一個小型齒輪加工單元自動上下料系統。機器 人 選 用 UR10 工 業 機 器人,有效負載 10kg,工作范圍可達 1300mm,接口兼容大多數工業傳感器及 PLC,支持以太網通訊; 采用 SIEMENS 數控系統的數控機床,機床卡盤與防護門均采用氣動控制方式,且設有工作到位檢測開關。系統布局如圖 2所示。
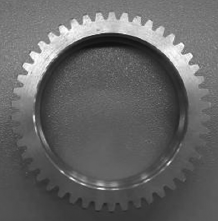
圖 1 工件實物圖
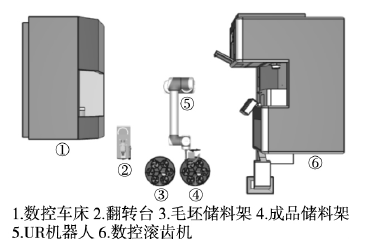
圖 2 系統整體布局
1. 2 工作過程規劃
根據加工單元技術要求及工藝特點,并結合加工單元結構組成,對工作過程進行規劃,如圖 3 所示。
考慮到加工單元初次工作時,數控車床內部并無成品完成件,因此需由機器人首次取料至車床加工,待加工完成后,由翻轉臺進行加工面更換,繼續上料數控車床,然后從毛坯儲料架繼續抓料。待前工件加工完成后,機器人雙手爪工作,進行車床上下料操作,滾齒機內部同樣無成品完成件,因此只進行一次車削完成件的上料操作。如圖中虛線框所示。
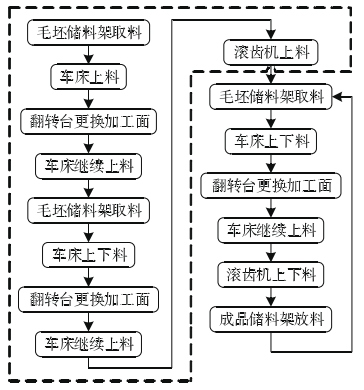
圖 3 系統工作流程
2、控制系統設計
2. 1 控制單元組成
系統包括數控車床、數控滾齒機、工業機器人、儲料架、翻轉臺 5 個控制單元。各控制單元完成動作后,須有相應的動作完成信號發出,從而通知系統下一步的動作。
為保證各控制單元的正常工作順序及控制邏輯的合理性,加工單元采用西門子 S7-1500 系列 PLC 作為主控制器,統一接收處理各控制單元的傳輸信號,協調各設備之間的動作響應。PLC 接有人機界面觸摸屏,實現對現場設備工作狀態的集中監控。翻轉臺及儲料架的動作由主控 PLC 控制,機器人與數控機床由自身集成的控制器控制,機器人、數控機床控制單元采用MODBUS-TCP 協議與主控 PLC 通訊。加工單元控制系統結構關系示意圖如圖 4 所示。
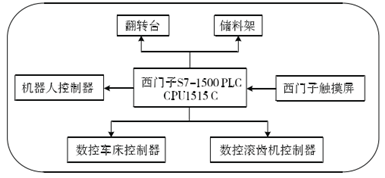
圖 4 控制系統結構關系示意圖
2. 2 通信系統建立
為提升系統整體結構的時效性,有效實現各設備之間的通訊連接,上下料系統需采用安全可靠、準確快速的通訊方式。
系統采用工業以太網通訊方式,將機器人、數控機床、主控 PLC、觸摸屏、終端計算機等進行通訊連接。其中機器人負責工件上下料示教編程,主控 PLC 除協調其他設備之間的信息交互,還控制翻轉臺及儲料架的動作。觸摸屏用于工作狀態的監控、提示。終端計算機負責程序的編程與調試。網絡通信系統結構如圖 5 所示。
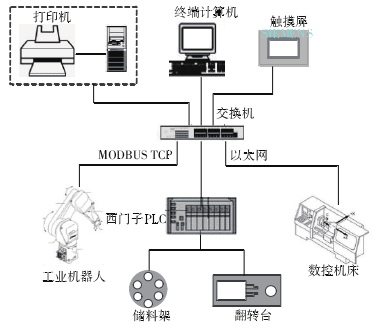
圖 5 通信系統結構
2. 2. 1 MODBUS TCP 通信協議
MODBUS-TCP 通信協議是運行在 TCP / IP 上的一種通信傳輸協議,利用該協議構建的以太網絡具有成本低,通訊高效、穩定,簡單易用等特點,可實現設備與設備之間,設備與網絡之間的有效通訊,因此廣泛應用于工業控制領域。本系統中,主控 PLC、機器人、數控機床控制器等均集成以太網接口,可通過 MODBUS-TCP 通信協議實現通訊連接。數據傳輸建立之前,MODBUS-TCP 通信協議需確定設備之間的邏輯關系,并建立 MODBUS 與 PLC 間的響應地址,從而保證通信的正常穩定。
2. 2. 2 主控 PLC 與機器人通訊
調用西門子 TIA Portal 軟件內嵌的 S7-1500 MOD-BUS-TCP 庫函數實現主控 PLC 與機器人的以太網通信,完成設備間的參數配置及狀態讀寫。主控 PLC 作為MODBUS-TCP 客戶端發送讀寫請求,服務端機器人負責請求的響應。
為保證主控 PLC 正確地發送和接收機器人數據,MODBUS-TCP 通信必須設計好兩者之間的數據讀寫區域。通信數據以字節為單位存儲于設備寄存器中,以字作為傳輸單位,以位為尋址單位。以 PLC 讀取機器人狀態數據為例,通過“機器人狀態字”讀取函數,將機器人內部輸出變量 SYSTEM /DO0 對應的 MODB-US 地址開始的 4 個字,讀入主控 PLC 并存放在 P #M3000. 0 開始的 4 字中; 當 PLC 發送數據至機器人時,“機器人控制字”函數工作,將 P#M3100. 0 中的開始 4個字 節 寫 入 機 器 人 輸 入 變 量 SYSTEM /DI0 對 應 的MODBUS 地址開始的 4 個字節中。主控 PLC 讀取和寫入機器人部分信號見表 1。
表 1 主控 PLC 讀取和寫入機器人部分信號表
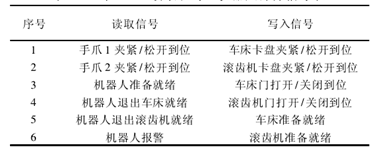
IP 地址分配是使用 MODBUS-TCP 通信的必須步驟,要保證所有設備網絡地址必須在同一網段內。利用 TIA Portal 為系統各個硬件分配 IP 地址,主控PLC IP 地址為 192. 168. 8. 10,機器人 IP 地址為 192.168. 8. 103。
明確了機器人與主控 PLC 之間讀寫信號及相關參數設定,分配各設備 IP 地址后,調用“MB_CLIENT”通信指令,實現客戶端與服務端之間的數據讀寫通信連接。編制的 MODBUS-TCP 通訊程序如圖 6 所示。
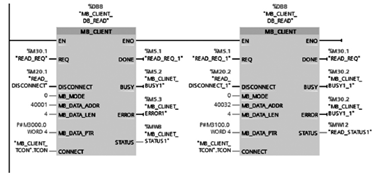
圖 6 主控 PLC 與機器人通訊程序
3、機器人上下料程序設計
3. 1 機器人上下料路徑規劃
機器人要完成在儲料架、數控機床、翻轉臺之間的上下料工作,移動路徑多樣,有必要對機器人上下料運動路線進行設計。根據系統結構布局,利用 UR 機器 人 示 教 編 程,規劃的機器人上下料路線圖如圖7 所 示。 設 計 過程 中,為 減 小 機器 人 與 儲 料 架、機床夾具之間的配 合 偏 差,固 定配 合 移 動 方 向,保證工件持續裝夾作業的一致性,需在機器人上下料處設置不同的 TCP 坐標點,即建立不同的工具坐標系。
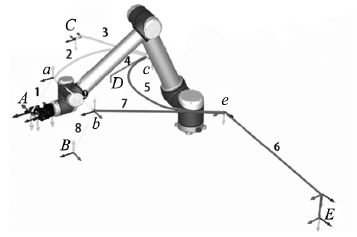
圖 7 機器人上下料路徑
圖中 A、B 兩點為毛坯抓取點與成品放置點,a、b為上下料的初始準備位置; C、D、E 分別為數控車床、翻轉臺、數控滾齒機的工件裝夾處,c、e 分別為機器人與數控機床之間上下料的初始準備位置。
3. 2 機器人上下料流程設計
根據機器人上下料路徑規劃,設計的機器人運動流程圖如圖 8 所示。
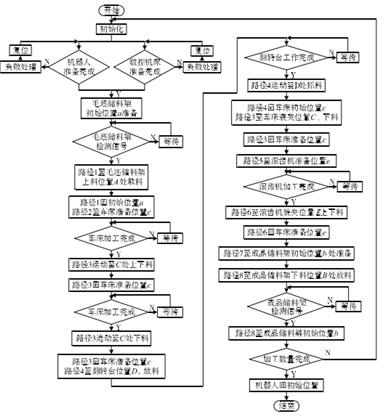
圖 8 機器人運動流程
3. 3 機器人上下料程序編程
Polyscope 編程為 UR 機器人 UI 層編程方式,示教器上編輯程序,機器人執行,編程方式簡單,程序易于調試、修改。根據機器人的軌跡規劃及上下料流程,編寫了機器人上下料程序。以機器人上下料數控車床運動程序為例,描述如下。圖 9 為機器人上下料數控車床現場圖。
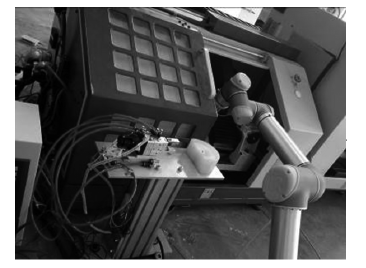
圖 9 機器人上下料數控車床
. . . . . .
LOOP 9 TIMES
MOVEJ Waypoint1; 機器人初始位置準備
Call Sub Program1: 機器人抓取毛坯件子程序
Call Sub Program2: 機器人上下料數控車床子程序
MOVEJ Waypoint4; 機器人至車床準備位置
Wait DI14 = HI; 等待車床加工完成信號
Wait DI6 = HI; 等待車床門打開到位信號
MOVEL Waypoint5; 手爪 2 至卡盤右側 5CM 處
MOVEL Waypoint6; 手爪 2 至工件裝夾處
Set DO1 = OPEN; 手爪 2 夾緊
Wait DI3 = HI; 等待手爪 2 夾緊到位信號
Wait DI12 = HI; 等待車床卡盤松開到位信號
MOVEL Waypoint5;
MOVEJ Waypoint7; 手爪 1、2 位置互換
MOVEL Waypoint6; 手爪 1 至工件裝夾處
Wait DI10 = HI; 等待車床卡盤夾緊到位信號
Set DO0 = CLOSE; 手爪 1 張開
Wait DI4 = HI; 等待手爪 1 張開到位信號
MOVEL Waypoint5;
MOVEL Waypoint4;
Wait DI8 = HI; 等待車床門關閉到位信號
Wait DI14 = HI; 等待車床加工完成信號
Wait DI6 = HI; 等待車床門打開到位信號
MOVEL Waypoint5;
MOVEL Waypoint6;
Set DO0 = OPEN; 手爪 1 夾緊
Wait DI2 = HI; 等待手爪 1 夾緊到位信號
Wait DI12 = HI; 等待車床卡盤松開到位信號
MOVEL Waypoint5;
MOVEL Waypoint4;
Call Sub Program3; 機器人上料翻轉臺子程序
Call Sub Program4; 機器人上料數控車床子程序
Call Sub Program5; 機器人上下料滾齒機子程序
Call Sub Program6; 機器人下料成品件子程序
MOVEJ Waypoint1;
對企業布局的 6 處小型齒輪加工單元進行加工試驗,分別加工齒輪 20 件,與人工作業相比,自動上下料系統加工效率得到顯著提高,產品穩定性得到進一步改善。對比結果見表 2。
表 2 自動上下料系統與人工作業對比
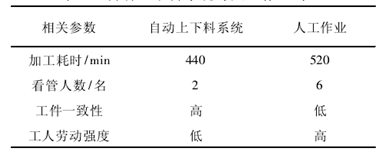
4、結束語
在“智能制造”的發展規劃下,小型齒輪加工單元自動上下料系統的設計為中小企業自動化程度及競爭力的提高提供了新思路。現場加工試驗表明:
(1) 通過合理布局自動上下料系統,可有效地節省人力資源及企業用工成本,提高中小企業加工效率;
(2) 自動上下料系統具有較高的重復定位精度,成品件一致性較人工作業得到大幅度提高;
(3) 系統采用西門子 S7-1500PLC 作為主控制器,通過 MODBUS-TCP 通信協議,實現了工序間的信息流、工序轉換的自動化,布局簡單,調試方便。
投稿箱:
如果您有機床行業、企業相關新聞稿件發表,或進行資訊合作,歡迎聯系本網編輯部, 郵箱:skjcsc@vip.sina.com
如果您有機床行業、企業相關新聞稿件發表,或進行資訊合作,歡迎聯系本網編輯部, 郵箱:skjcsc@vip.sina.com